Viscoelastic properties of liquid lubricants can offer unexploited insights into innovative ways to develop additives for applications such as engine oils. As industries face increasingly stringent emissions regulations, improving fuel efficiency has become more crucial than ever. Leveraging these unexploited insights not only offers a pathway to improved emissions but can also provide insights into reducing wear and extending the lifespan of high-mileage engines.
At the Centre for Industrial Rheology, we have been exploring the use of viscoelastic measurements, namely normal stress, for liquid lubricants. This case study investigates the impact normal stress has on the load-carrying capacity and showcases how we can utilise our axial testing capabilities to capture normal stress measurements.
Impact of Normal Stress on Load-Carrying Capacity
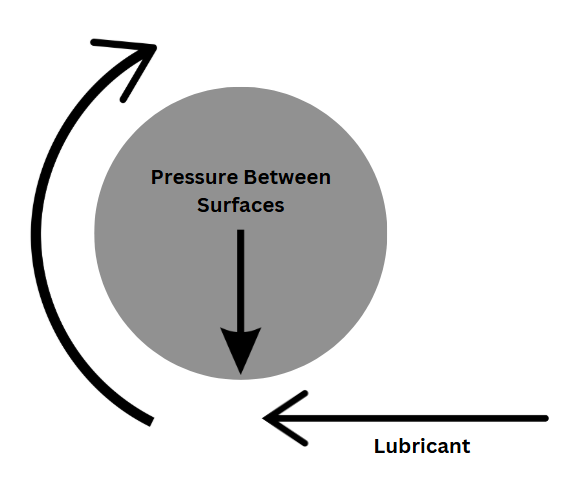
Hydrodynamic Lubrication and Film Thickness
Hydrodynamic lubrication is where a lubricant film separates two moving surfaces, reducing metal-to-metal contact and minimising wear, and energy losses due to friction. It is imperative to ensure the resulting hydrodynamic film thickness of liquid lubricants is sufficient to prevent metal-to-metal contact under operating conditions.
Load-Carrying Capacity
The load-carrying capacity refers to the ability of the lubricant film to support a load between the two surfaces without them coming into contact with each other. Increasing the load capacity of liquid lubricants is a key consideration when developing polymer additives for engine oils. The most intuitive way to increase the load capacity is to increase the viscosity of the lubricant, which results in an increased hydrodynamic film thickness. A key problem arises with this, as increasing the viscosity of the lubricant incurs a frictional penalty and reduces efficiency. Ideally, you would want to increase the load-carrying capacity without causing this frictional penalty, such that you can achieve a balance between high load capacity and low friction.
There is compelling evidence that this may be possible. A study by Elsharkawy on the effects of lubricant additives on the performance of hydrodynamically lubricated journal bearings demonstrates that lubricant additives can simultaneously increase load-carrying capacity and reduce the friction coefficient [1].
Normal Stress
An often-underexplored area is to look at the effect that normal stress has on increasing the load-carrying capacity. The normal stress is the force per unit area exerted perpendicular to the surfaces in contact with the lubricant film. It has been reported by Bair that “the normal stress difference can increase the load capability of a lubricant film without increased frictional penalty” [2]. This insight holds particular significance, prompting us to investigate this further.
Normal Stress Measurements using a Shear Rate Sweep
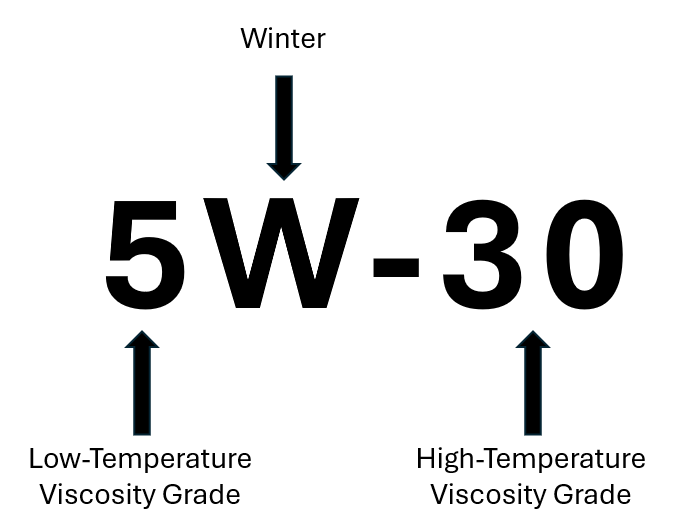
At the Centre for Industrial Rheology, we can conduct shear rate sweeps utilising our rotational rheometers. Traditionally, these are used to measure viscosity as a function of shear rate, however, we can extend this with our axial testing capabilities to measure the normal stress as a function of shear rate as well.
We conducted a case study on three different engine oils with different viscosity grades to measure the normal stresses as a function of shear rate. Viscosity grades indicate an oil’s flow characteristics.
The three engine oils we tested were:
- GoldenFilm SAE50 – A monograde mineral oil, specifically made for naturally aspirated four-stroke petrol and diesel engines with a distinct characteristic of low detergent/dispersant lubricants.
- Carlube 15W-40 – A multigrade mineral oil, with extensive additives marketed as exhibiting especially strong wear protection.
- Castrol 5W-30 – A multigrade fully synthetic oil, and the most popular engine oil for modern cars containing many additives and focused on delivering more power whilst improving engine efficiency.
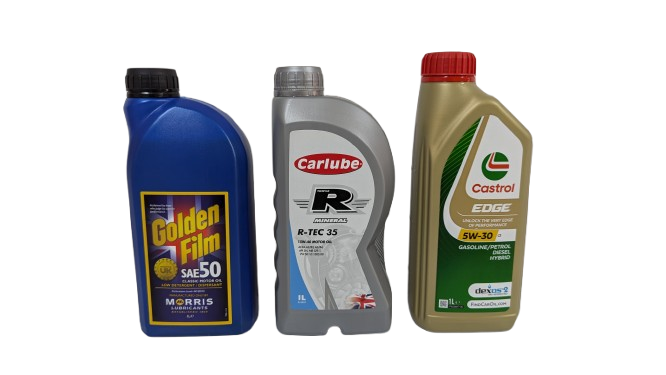
Based on the viscosity grades, Castrol 5W-30 flows easier at cold temperatures when compared to Carlube 15W-40, which is slightly thicker and is better at maintaining film strength to protect engines at higher temperatures. SAE50 does not have a “W” rating as it is a monograde oil and is measured based on its viscosity at high temperatures.
Shear Rate Sweep Results
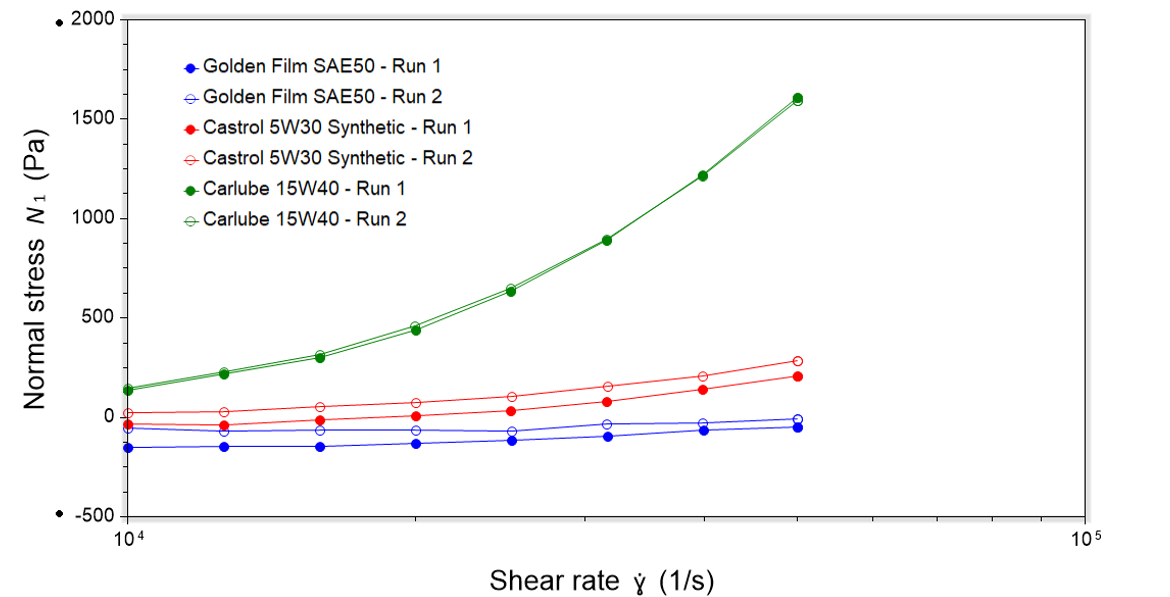
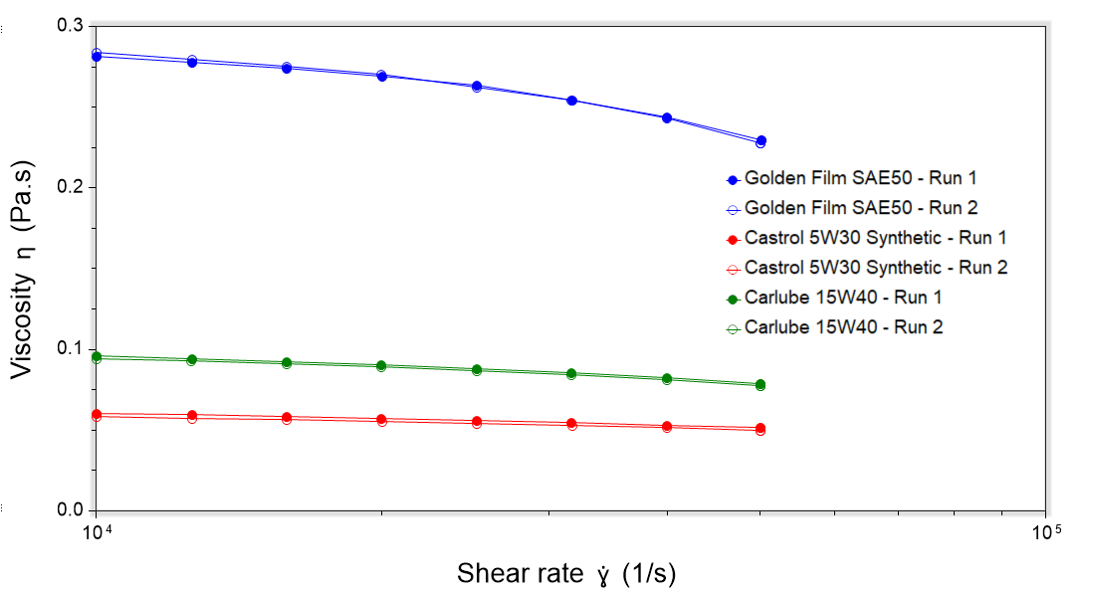
GoldenFilm SAE50
If looking solely at the viscosities, we would expect the GoldenFilm to exhibit the highest normal stress values when compared to the other oils due to the thicker hydrodynamic film. However, when you factor in that it has much lower additive content compared to its counterparts, the fact that it exhibits the lowest normal stress values compared to its counterparts shows further how additives may play a key role in increasing the normal stress.
CarLube 15W40
The CarLube exhibits the highest normal stress values out of all the oil samples, showing a significantly more pronounced increase as the shear rate increases. This oil is marketed as having “especially strong wear protection” and boasts the fact that it has 64% less cylinder wear than the ACEA A3/B4 test limits. Interestingly, the CarLube’s viscosity is only slightly higher than Castrol, yet still exhibits a much greater normal stress. This suggests that the normal stress of the CarLube could be significantly contributing to the load capacity and hence the marketable wear protection.
Castrol 5W30
The Castrol shows a slightly higher normal stress than the GoldenFilm. The high additive content of the Castrol can explain why it still exhibits higher normal stress than the GoldenFilm despite having a much lower viscosity. The Castrol’s aim is to ensure greater power delivery whilst also improving engine efficiency, with a strong focus on improving vehicle emissions as worldwide emissions regulations tighten. It could be interesting to see the role that normal stress measurements have in developing engine oils to reduce emissions.
Summary
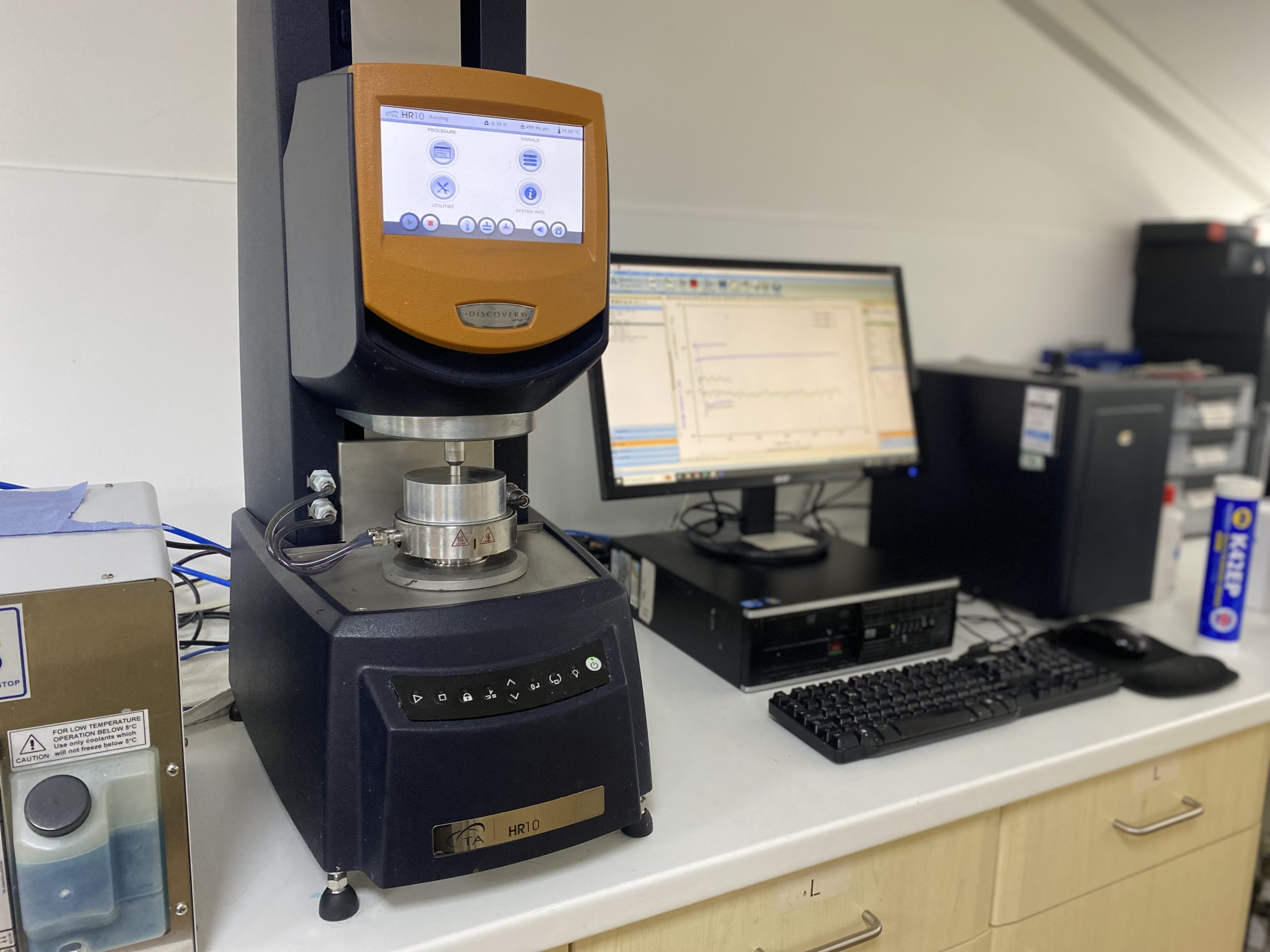
Utilising our rotational rheometers’ axial testing capabilities, we were able to generate normal stress data for three different engine oils and investigate the potential significance of this data for the development of polymer additives. Although the contribution of normal stress is more focused on reducing wear, if you can increase the load capacity without increasing viscosity, there is potential to engineer an oil to exhibit a lower viscosity and have the same load capacity when compared to an oil with a higher viscosity.
Contact us if you are keen to explore how we can exploit our testing capabilities for normal stress measurements. In addition to normal stress measurements, we offer oscillatory thermorheology profiling to offer rapid and powerful insights into low-temperature gelation phenomena. Read our case study on lubricating oil gelation prediction with high-performance rheology where we performed thermorheological profiling on the same three engine oils.
References
[1] – Elsharkawy AA. Effects of lubricant additives on the performance of hydrodynamically lubricated journal bearings. Tribology Letters. 2005 Jan;18:63-73.
[2] – Bair S. The first normal stress difference in a shear-thinning motor oil at elevated pressure. Tribology Transactions. 2015 Jul 4;58(4):654-9.