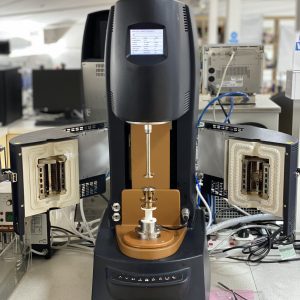
High-temperature rheology measurements are useful for materials such as oils, plastics, resins, greases, and binders or to characterise the behaviour of feedstock in high-temperature industrial processes such as cooking, pasteurisation or any thermally accelerated chemical reaction. Many materials which are typically very tough or rigid at room temperature can undergo softening or melting as temperatures are increased. In the world of thermoplastics, this is useful as it enables reforming the material to a desired shape. Identifying the melting point of a material is useful for identifying a temperature at which it becomes easier to handle, but a material may also go through other non-phase transitions. For example, the glass transition is a point where some materials transition from a relatively brittle ‘glassy’ state to a rubbery, viscous state. Our lab provides testing, training, and consulting to companies within the pharmaceutical, food, cosmetic, petrochemical, electronics, automotive, aerospace and construction industries looking to better understand the physical properties of their products, including temperatures up to 500°C.
If you would like to discuss characterising the rheological properties of your materials at elevated temperatures, please feel welcome to contact us.
Viscosity Profiling
Viscosity is a key metric for understanding a material’s flow behaviour during pumping, mixing, filling and general handling. In high-temperature rheology measurements, typical rotational shear viscometers may not be practical for measuring viscosity due to the difficulty in heating a sample evenly or applying uniform shear. Our rheometers can work with much smaller samples and under a vast range of shear rates and shear stresses helping to better understand how a material may behave in a dynamic situation, such as initial pump start-up to full flow.
Oscillatory Frequency Sweeps
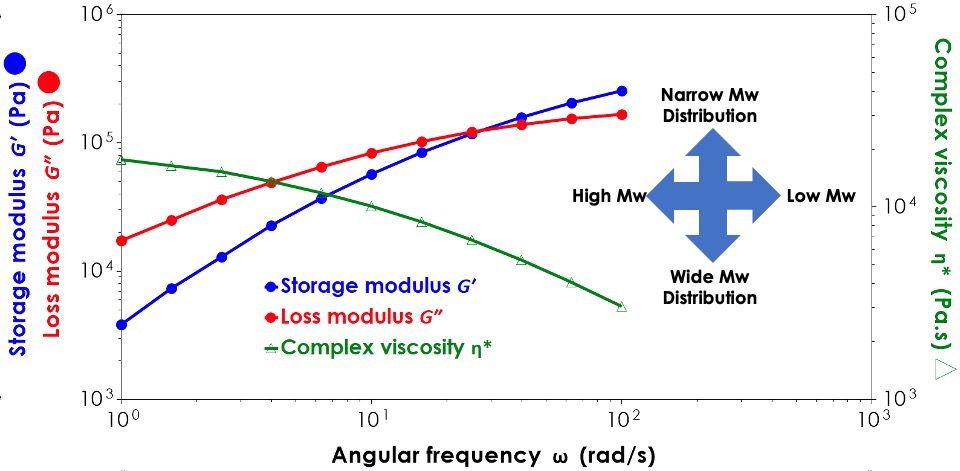
Oscillatory sweeps are the method of choice for high-temperature rheology work where viscoelastic properties are of interest, where high shear rates may not be practically obtainable or where structural or low shear behaviour is of most interest. An oscillatory rheometer gently wobbles a sample back and forth measuring either the stress required to reach a target deformation value or, how far the rheometer has to push when attempting to reach defined stress (known as stress controlled and strain controlled respectively). In a frequency sweep, the stress/strain response to deformation is measured as a function of the frequency of oscillation, specifically to probe for time-dependent/frequency-dependent viscoelastic properties. Silly putty is an extreme example to show how a material changes its behaviour depending on the timescale of deformation – over time it will ooze out under its own weight, but if you collect it and ball it up, it can bounce as if it were solid rubber. Polymeric materials, such as silly putty, can display similar behaviours to a more or lesser degree – they behave as elastic solids under short timescales of deformation, and over long timescales behave as if they were a viscous liquid.
Complex Modulus, Elastic Modulus, Viscous Modulus and Tan Delta
In simple terms, the complex modulus is a measure of the overall stiffness or rigidity of a material and is given by dividing a given stress over a given strain. A material that ‘bounces back’ or recovers elastically is assumed to have presented some kind of inherent elastic structure. If the material is unable to revert to its former condition following the applied deformation, then some permanent or ‘viscous’ deformation has occurred. These concepts form the basis of the elastic or storage modulus, which is a measure of the elastically recoverable deformation of the sample, and the viscous or loss modulus, a measure of the permanent deformation in the sample. Tan delta is a measure of viscoelastic dominance or dampening within a material and is given by dividing the loss modulus by the storage modulus. A tan delta value of one indicates that the viscous modulus is the larger component of the overall complex modulus. For a beginner’s guide to storage and loss modulus, check out our video by clicking on this link.
High-Temperature Rheology and Stability
An increase in temperature generally tends to accelerate chemical reactions. Indeed simply cooking an egg can showcase the degree to which temperature can significantly and irreversibly change material handling properties. A temperature hysteresis ramp involves increasing the temperature to a set target before coming back down to ambient or a lower target temperature. Comparing the up-sweep and down-sweep can give indications of thermal lag, but also repeat measurements can identify the robustness of the material. Alternatively, it is possible to simply hold the material at an elevated temperature and look at how its rheological properties change over time.
Time Temperature Superposition (TTS)
Despite the versatility of oscillatory frequency sweeps, researchers are limited to the sensitivity of the equipment they are using and oftentimes viscoelastic behaviour over very short or very long timescales is of key interest. The time-temperature superposition (TTS) principle is a general concept that implies a relationship between temperature and the time-dependent response of a polymer. TTS can be used on thermorheologically simple polymers to generate ‘master curves’ at specified reference temperatures, which can describe the viscoelastic properties of a material at a single temperature over a vast frequency range.
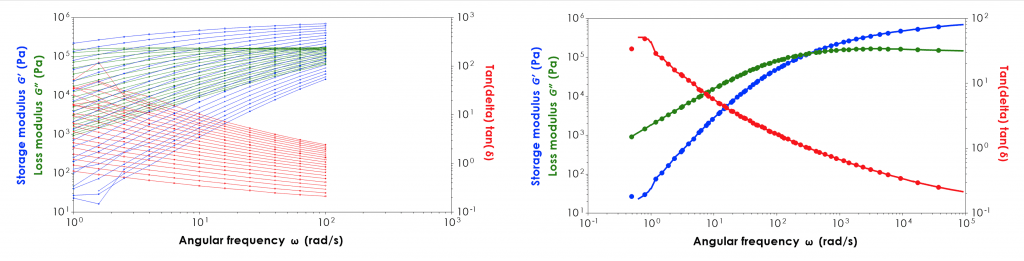