Stirring a graphene ink for electronic screen-printing reveals that a potentially significant rheology behaviour may be missing from the Certificate of Analysis. We identified two properties serving as crucial indicators for those refining their printing procedures with specialised screen printing ink.
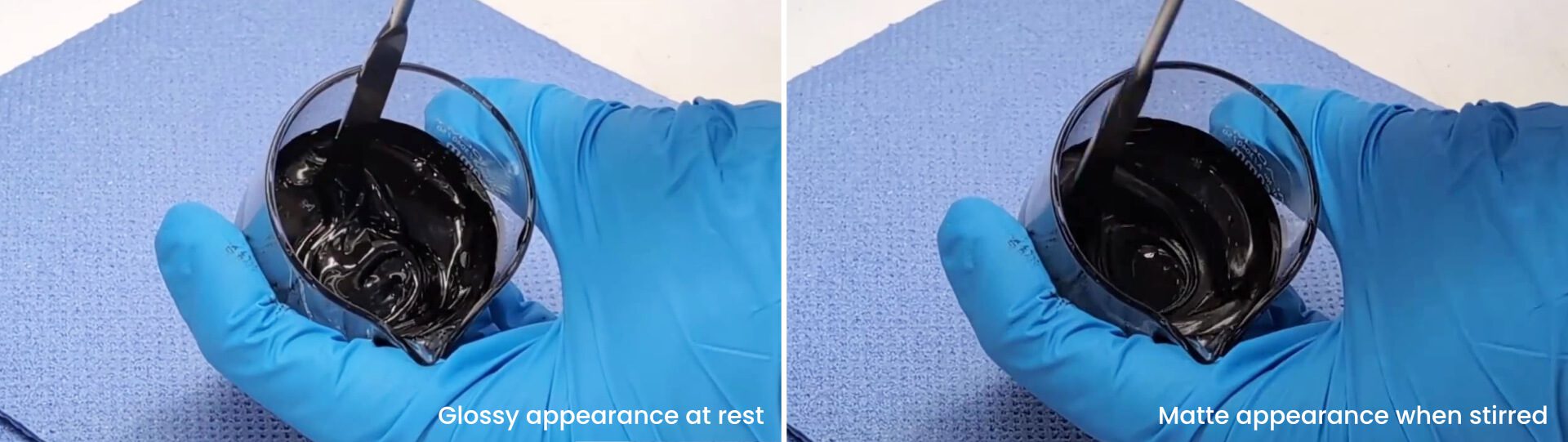
Contact us to discuss the characterisation of your screen printing inks
Why is the Rheology of a Screen-Printing ink Crucial to Electronic Innovators?
Screen printing stands as a popular method for depositing conductive or resistive inks or pastes in the manufacturing of printed electronics. The rheology of screen-printing materials, including shear thinning behaviour, thixotropy, and the presence of a yield stress, all play a pivotal role in determining the speed and efficiency of a process. Having accurate and reliable data on these rheological aspects is crucial for electronic manufacturing; the Centre for Industrial Rheology believes that innovators shouldn’t lose valuable time over a lack of crucial rheological data.
Insights into the Viscosity of the Screen-Printing Paste.
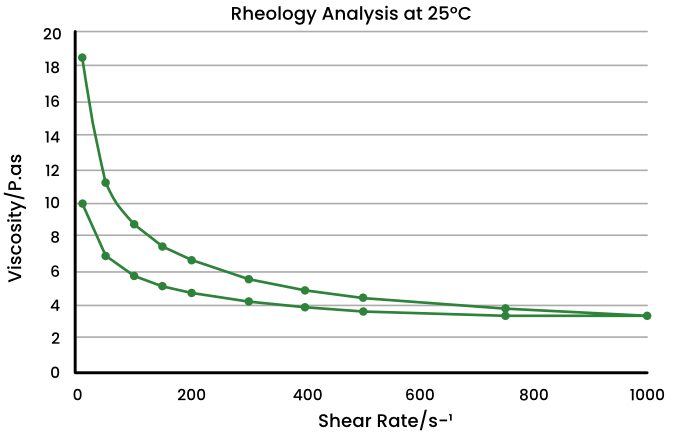
The viscosity portion of the Certificate of Analysis provided by the manufacturer of the screen-printing ink demonstrates shear-thinning behaviour, meaning the ink’s viscosity decreases with increasing shear rate. However, interacting with the ink suggests the opposite; when the ink is stirred, it loses its gloss, and more force is required to continue stirring. These physical characteristics suggest shear-thickening.
If the ink exhibits shear-thickening behaviour during handling, it is expected to maintain this characteristic under test conditions and even in its use within the screen-printing process. Our investigation aims to delve into other rheological parameters to elucidate the underlying behaviours responsible for the shear-thickening appearance of a shear-thinning screen-printing ink.
Likening the Ink’s Behaviour to the Wet-Sand Effect
To understand shear-thickening, a material whose viscosity increases upon the application of force, we can use the wet-sand effect as an example.
The combination of water and sand on the beach forms a suspension which, when gently picked up, behaves akin to flowing custard between your fingers. However, when pressure is applied, the sand appears dry and solid. This phenomenon, known as the wet-sand effect, arises when, under the application of external force, solid particles must manoeuvre around one another. The net result of the jostling particles is that the wet mass increases in volume (dilates) and the particles jam against each other, increasing the resistance to flow (viscosity).
Like wet sand, screen-printing inks and pastes comprise various components forming a suspension. Whether water or solvent-based, these inks may consist of diverse solid particles like gold, silver, or pigments, along with binding chemicals. However, the suspension composition marks an end in the comparison of screen-printing inks to wet sand. The shear-thickening behaviour suggested by the handling of the ink is proving elusive, which demonstrates that shear viscosity alone proves inadequate in fully characterising the ink’s rheology.
Exploring other Rheological Parameters of the Screen-Printing Ink
In our investigation of the Certificate of Analysis, our technicians ran a shear rate sweep viscosity profile using the DHR 2 by TA Instruments and obtained largely similar results to the manufacturer’s Certificate of Analysis. By this juncture, it became apparent that, while the Certificate of Analysis revealed the shear viscosity, it omitted other factors crucial to understanding the ink’s behaviour.
We re-ran the viscosity test, but also followed another rheological parameter: normal stress. Normal stress is a perpendicular (i.e. normal) stress generated when some materials are sheared. A significant increase in normal stress is observed in the screen-printing ink, suggesting that the ink sample is dilating, attempting to push apart the cone and plate of the rheometer.
Understanding the normal stress reveals that the physical characteristics displayed when interacting with the screen-printing ink aren’t a reflection of its shear viscosity; the liquid phase of the suspension is moving into the vacant areas within the wet mass caused by dilation, owing to the normal stress.
Oscillation Stress Sweep Test: Understanding the Structure of the Screen-Printing Ink
To further study the rheology of the screen-printing ink and to obtain a greater understanding of the physical characteristics our lab technicians saw when interacting with the material, we performed an oscillation stress sweep test. Oscillatory measurements serve as an invaluable tool in examining intricate, soft structures that defy characterisation solely through viscosity assessment.
One of the rheological parameters understood by an oscillation stress sweep test is complex modulus: the resistance to deformation in a material. Typically, in inks we would expect to see a decrease in complex modulus as stress increases and the ink structure undergoes yielding. However, the results produced in our oscillation stress sweep test showed an increase in complex modulus at higher stresses.
Revealing the Rheological Property that Causes the ‘Thickening’ Behaviour in Screen-Printing Inks
Based on the complex modulus of the screen-printing paste, we are observing a phenomenon known as strain overshoot. Strain overshoot can be defined as an increase in modulus as more stress is applied to a material. This phenomenon is revealing the contradiction between the reduced shine and apparent thickening when handling the screen-printing ink against the viscosity behaviour presented in the Certificate of Analysis.
Those in the electronics industry employing this screen-printing ink would likely notice the absence of critical data in the Certificate of Analysis provided by the manufacturer. This data gap fails to depict the ink’s behaviour during its application in electronic production processes and could be detrimental to the manufacturing of electronics.
Conclusion
A difference in the viscosity of a screen-printing ink against how it behaves when handled quickly told us that shear viscosity alone is not adequate in fully characterising the rheology of a screen-printing ink. Upon subjecting the ink to further rheological tests, our lab deduced that what appeared to be shear-thickening was, in fact, strain hardening.
The conventional rheology tests performed by manufacturers often fall short in supplying adequate data for innovators utilising their materials. Innovators must understand the full scope of rheological parameters that impact their R&D or manufacturing procedures, and they must be able to rely on the data provided in the Certificate of Analysis. The Centre for Industrial Rheology plays a pivotal role helping innovators and manufacturers in saving time and resources by furnishing essential data and elucidating the various material characteristics crucial to their materials.
If you would like to learn more about other approaches to characterising the physical properties of your screen printing materials, please feel welcome to organise a talk with us.