Thermopolymers, thermoplastics or thermosoftening plastics have heat-sensitive rheological properties, such as a melt or crystallisation behaviour that enables vast utility of plastics in many industries such as packaging for food, pharmaceuticals and cosmetics to more general consumer goods and devices. The acute control of these rheological properties through regulation of temperature enables the manufacturer to shape and form the material to incredibly detailed and intricate designs, within a short space of time, reliably and repeatably.
If you would like to discuss characterisation of your polymer in the melt condition, then please feel welcome to get in touch.
Most industrial professionals are aware of the ubiquity of polymers and the myriad of forms that a polymer material can take on – key quality attributes of thermoplastics generally include stiffness, brittleness, hardness, ductility, thermal sensitivity and extensional properties. Our lab specialises in characterising the fundamental physical properties that determine many key quality attributes of thermopolymers such as the glass transition temperature, youngs modulus, elastic modulus, viscous modulus, tan delta and now thermal conductivity. If you would like to better understand the rheological properties of your thermopolymer as a function of temperature or would like to discuss how we can help you, then please feel welcome to contact us.
Visualising Polymers – Snakes, Spaghetti and Springs
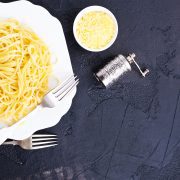
Many of the observed behaviours we see in polymers are as a direct result of molecular structure and interactions between individual polymer chains. An idealised and simplified view of what causes increases in viscosity would be that the longer the polymer chains, the more opportunity of entanglement and inter-chain ‘friction’ between two or more molecules – think of the differences between a bowl of macaroni or penni versus a bowl of spaghetti or linguine.
Polymer chain tacticity, branching, flexibility, charge density and elasticity can complicate matters as this may improve or weaken inter-chain attraction/repulsion and entaglement, but it is also important to remember that when molten, polymers are in a fluid state and moving around. If the material cools before the chains can relax or relieve stresses introduced from handling, these can become frozen into the structure of the material causing unexpected behaviours during product use.
For example, Linear Low-Density Polyethylene (LLDPE) generally is formed of relatively short chains of polyethylene and has a lower melting point, lower tensile strength, lower flexural strength, lower density, high transparency and high shrink rate in comparison with High Density Polyethylene (HDPE) which contains the same repeating monomer unit, in much longer chains.
Since rheology is so sensitively linked to processes occurring at the molecular scale, this can make it an excellent practical tool for quick investigations for both understanding bulk handling behaviour and the fundamental chemistry affecting it.
Melt viscosity and elasticity of thermoplastics – Non-Newtonian behaviour
Molten polymers are typically non-Newtonian, meaning their viscosity changes as a function of applied shear. Since shear rates can vary throughout even across a single unit process, predicting material behaviour is of vital importance to the process engineer. However, shear measurements on molten polymers are challenging – edge failure, a situation where the sample leaves the gap due to normal forces induced by high shear, is a common limiting factor when performing direct shear measurements. High strain rates can also irreversibly damage the sample by untangling and tearing the sample, destroying any inherent structure which may be the subject of interest for example during stability studies.
Oscillatory measurements involve gently wobbling a sample back and forth at a defined frequency measuring either the degree of deformation (strain) or the amount of resistance encountered (stress) when attempting to deform the material using a predetermined amount of stress or strain. Oscillatory measurements are typically used to measure the modulus (stiffness) of a material, however mathematical transformations, such as the Cox-Merz equation applied to oscillatory data, can enable the prediction of viscosity-shear rate dependent behaviour with minimal disruption to the polymer’s structure.
Oscillatory testing provides additional benefit over other methods such as capillary rheometry or torque measurements in-situ as it can help characterise viscoelastic properties that determine die swell and injection moulding behaviour. As we’ll learn below, these viscoelastic properties can be used to understand several vital properties of polymers.
Zero shear viscosity and Molecular Weight
“Zero shear viscosity” is the viscosity of the polymer melt measured under ‘at rest’ conditions or within the linear viscoelastic region. Under low shear conditions the melt viscosity of a thermoplastic is mainly determined by the molecular weight of the polymer. For ‘low molecular weight’ polymers which are untangled, the zero-shear viscosity is directly proportional to the polymer sample’s molar molecular weight at a 1:1 ratio. Above a critical molecular weight, polymer entanglement becomes much more likely which manifests in a very sharp increase in zero shear viscosity. Generally for each small increase in molecular weight, the zero shear viscosity increases significantly at a ratio of 1:3.4 making it a sensitive and practical alternative to other methods such chromatography.