Measuring the foaming ability of products can provide valuable insights into product behaviour. In the case of laundry detergents, being able to compare different brands against each other and measure how water hardness affects foamability and foam stability is very useful as it allows for benchmarking. This case study showcases the use of dynamic foam analysis to compare a leading-brand of liquid laundry detergent with a supermarket-own brand version. In addition, we also probe the effects of hard and soft water on foaming behaviour using a Krüss Dynamic Foam Analyser (DFA100).
Contact us to arrange a lab tour and discuss foamability and other rheological techniques with our experts
Dynamic foam analysis is a powerful technique that enables interrogation of foaming behaviours. Parameters such as foam height, drainage and foam stability can all be determined, allowing products to be directly compared and benchmarked. One family of products where foaming is a key characteristic is laundry detergents. The first commercially available laundry powder was developed by Henkel and launched in the UK in 1909. Laundry detergents are either powders or liquids and can be either biological (contain enzymes) or non-biological (without enzymes). Laundry detergents often contain water softeners, surfactants, bleaches, perfumes and foaming/anti-foaming additives. Biological laundry detergents also contain enzymes.
The foaming properties of a laundry detergents are extremely important. Too much foam can lead to poorly washed clothes that may need re-washing. This is due to the suds preventing clothes from rubbing against each other and undergoing cleaning through friction. In addition, too much foam can prevent the washing machine from draining water or lead an overflow of suds from the washing machine itself, resulting in flooding. On the other hand, lack of foaming can also be a problem. Although foaming itself does not necessarily clean a product, the formation of foam allows the formula to adhere to surfaces and enables penetration of the active substances. In addition, the fact that foam is adhered to a surface allows oils to be drawn from the surface via capillary action, leading to enhanced cleaning properties.
Hard water and soft water are chemically significantly different. Hard water contains dissolved salts, commonly Mg2+ and Ca2+ ions, that interact with surfactants and inhibit foaming. In some cases, these ions can cause rapid collapse of foam and formation of scum on the surface of the water. To counteract this, laundry detergents contain softeners. These softeners are often sodium (Na+) salts, for example sodium citrate, or zeolites. The softeners exchange the Mg2+ and Ca2+ for Na+ in the solution, which is softer, and does not lead to limescale or soap-scum build-up.
In this study, the foaming characteristics of a market-leading brand and a supermarket-own brand liquid laundry detergent were compared. In addition, the foamability in hard and soft water were contrasted. Each detergent was prepared according to the hand-wash instructions on the packaging. The market-leading brand was prepared at a concentration of 13 mL detergent and 5 L water and the supermarket-own brand was prepared at a concentration of 25 mL detergent and 10 L water. The samples (50 mL) were added to the Krüss Dynamic Foam Analyser (DFA100) and sparged with air through filter paper for 30 seconds at 0.3 L min–1.
How hardness of water affects foam height, foam stability and foamability
Foamability and foam stability are well-known to be affected by the hardness of the water in which they are generated. The presence of calcium and magnesium ions in hard water prevents detergents from foaming, or when a foam is formed it is less stable. Although softeners in the detergent can mitigate against this to some degree, the water will still likely have an impact upon the foaming characteristics.
A poorly foaming product would generate foam with a smaller height under the conditions used when compared with a product that foams well. In relation to foam height, a small loss of height is not entirely unexpected as over time the foam undergoes drainage, will naturally compact and some bubbles will burst. However, a less stable foam would lose height more quickly, and to a greater extent, than a more stable foam.
To investigate the foamability of the products and the impact of water hardness, two solutions of each sample were prepared: the first used deionised water, so can be designated as ‘soft’, and the second used the local tap-water, which is designated ‘very hard’ by the local water company (299 ppm Ca2+). In hard and soft water, both the market-leading brand and the supermarket-own brand produced foam.
Solely considering the soft water samples, there were only slight differences in the experimental results. Both foamed well, but the supermarket-own brand formed a slightly taller foam that degraded more slowly than the market-leading brand, Figure 1. The differences when using the local, hard water were more stark. Both samples initially formed a foam that was similar in height to that seen with the soft water however, the rate of decay of each was considerably different and the supermarket-own brand foam decayed much more quickly than the market-leading brand. This clearly shows that the type of water used for laundry has an impact upon the foam’s stability.
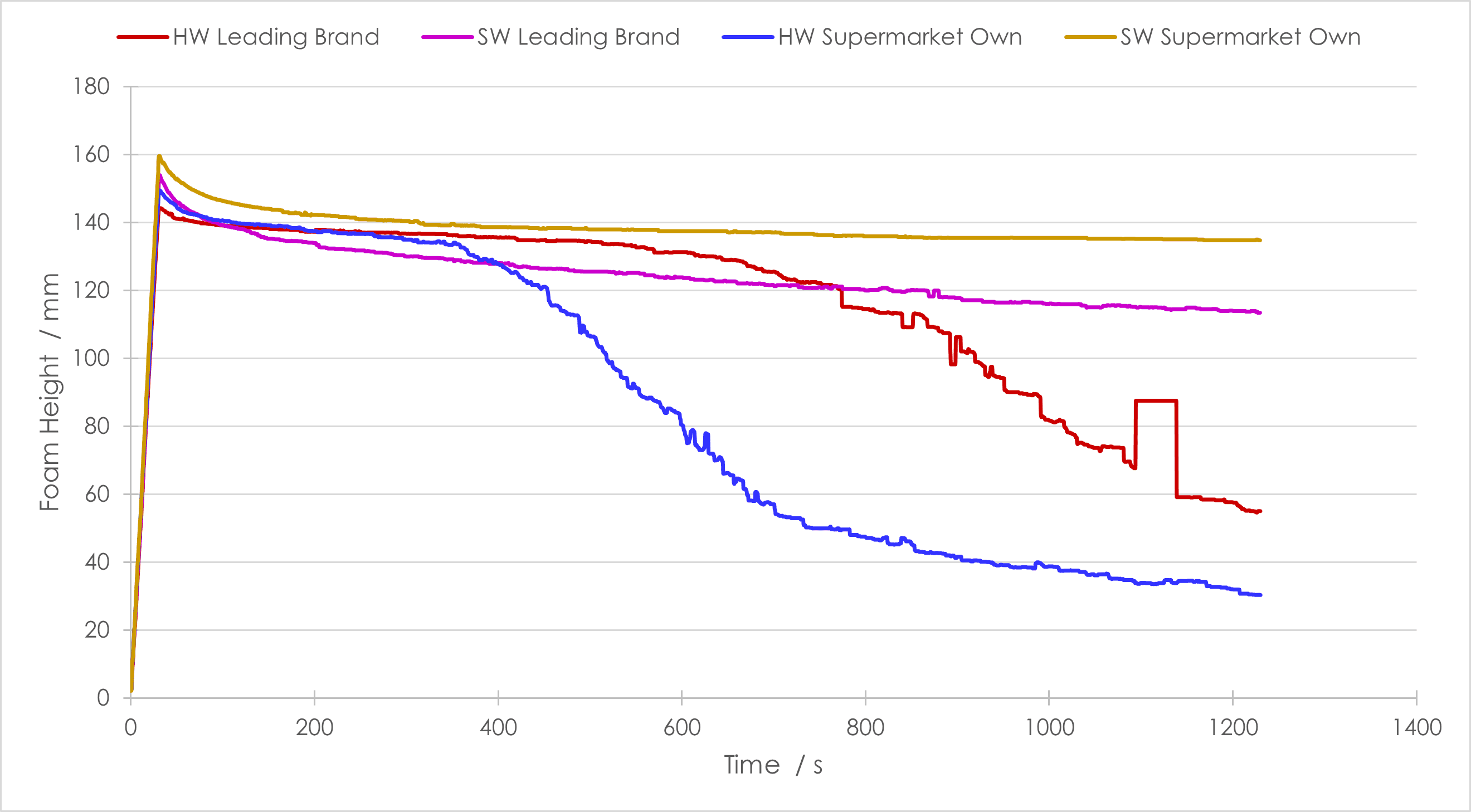
How hardness of water affects bubble count and mean bubble area
The effects of drainage and bubble size growth have a marked influence on the structure of a foam. In both cases, the bubble count decreased and the mean bubble area increased over the duration of the experiment, Figure 2. This is exactly what we would expect; as foams age the bubbles coalesce or merge through Ostwald ripening, giving larger bubbles. However, the rate at which this occurred during this experiment depended upon both the laundry detergent identity and the water used.
For bubble count and mean bubble area, the use of soft or hard water significantly impacted upon the data collected, Figure 2. In terms of bubble count, in soft water the supermarket-own brand and the leading-brand showed similar absolute bubble counts and rates of decay, therefore differences between the brands were not easily identified. In hard water, initially the supermarket-own brand gave more bubbles than the leading-brand, but both underwent rapid decay and in both cases the number of bubbles generated was significantly lower than in soft water, showing that the hardness of water impacts upon bubble generation. Overall, soft water led to a significantly higher bubble count and a slower rate of bubble decay compared to hard water.
In terms of mean bubble area, comparatively the soft water led to a smaller mean bubble area and the hard water a larger mean bubble area over the experiment. Comparing the soft water samples, both the supermarket-own brand and the leading-brand showed a similar rate of increase in mean bubble area and bubble size over the experiment, therefore differences were not identified. However, in hard water the differences between the samples were stark, and the leading-brand formed larger bubbles more rapidly than the supermarket-own brand.
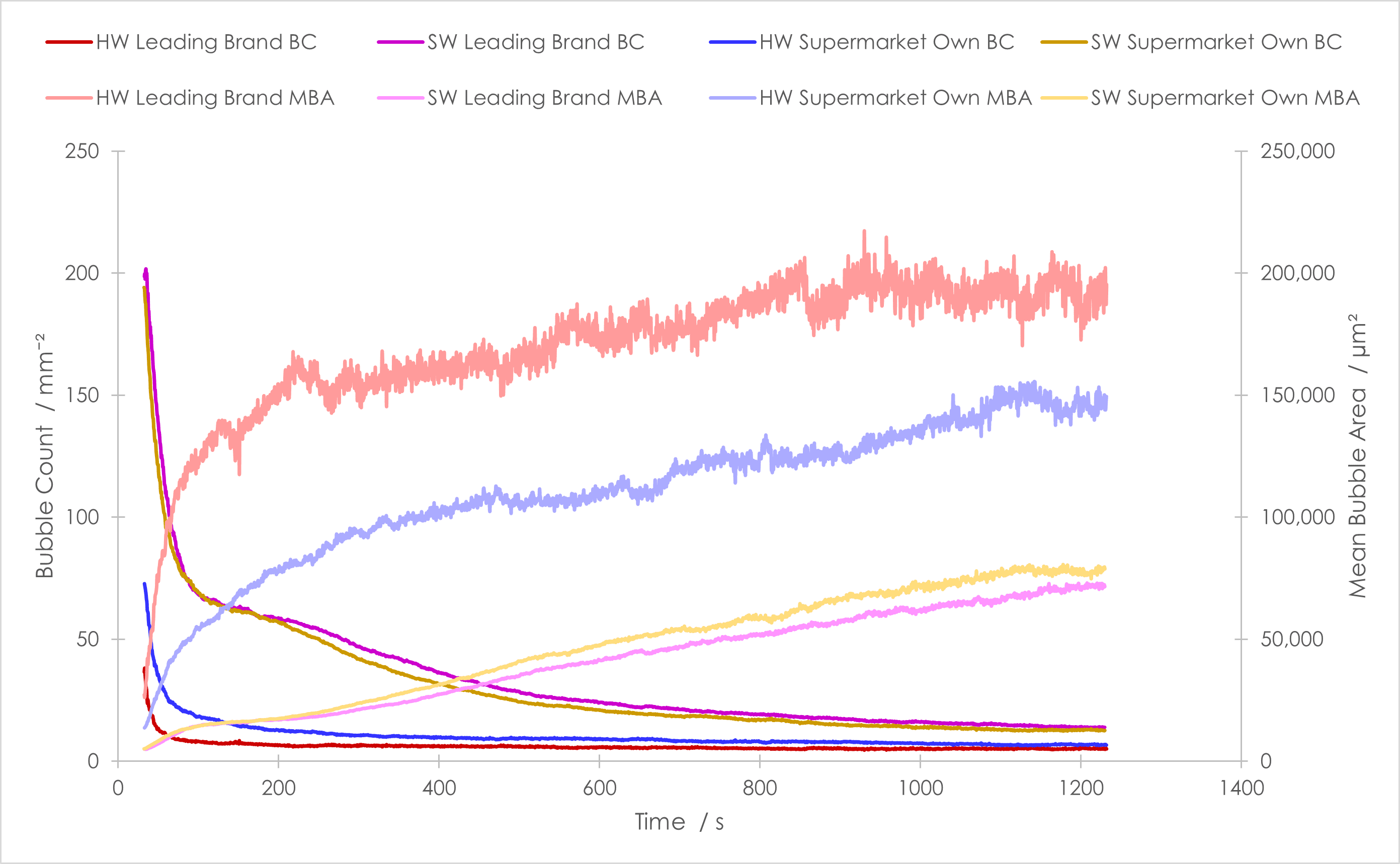
The bubble count and mean bubble area can also be observed by imaging during the experiment. Using these images, the differences between the samples can be clearly seen, Figures 3 and 4.
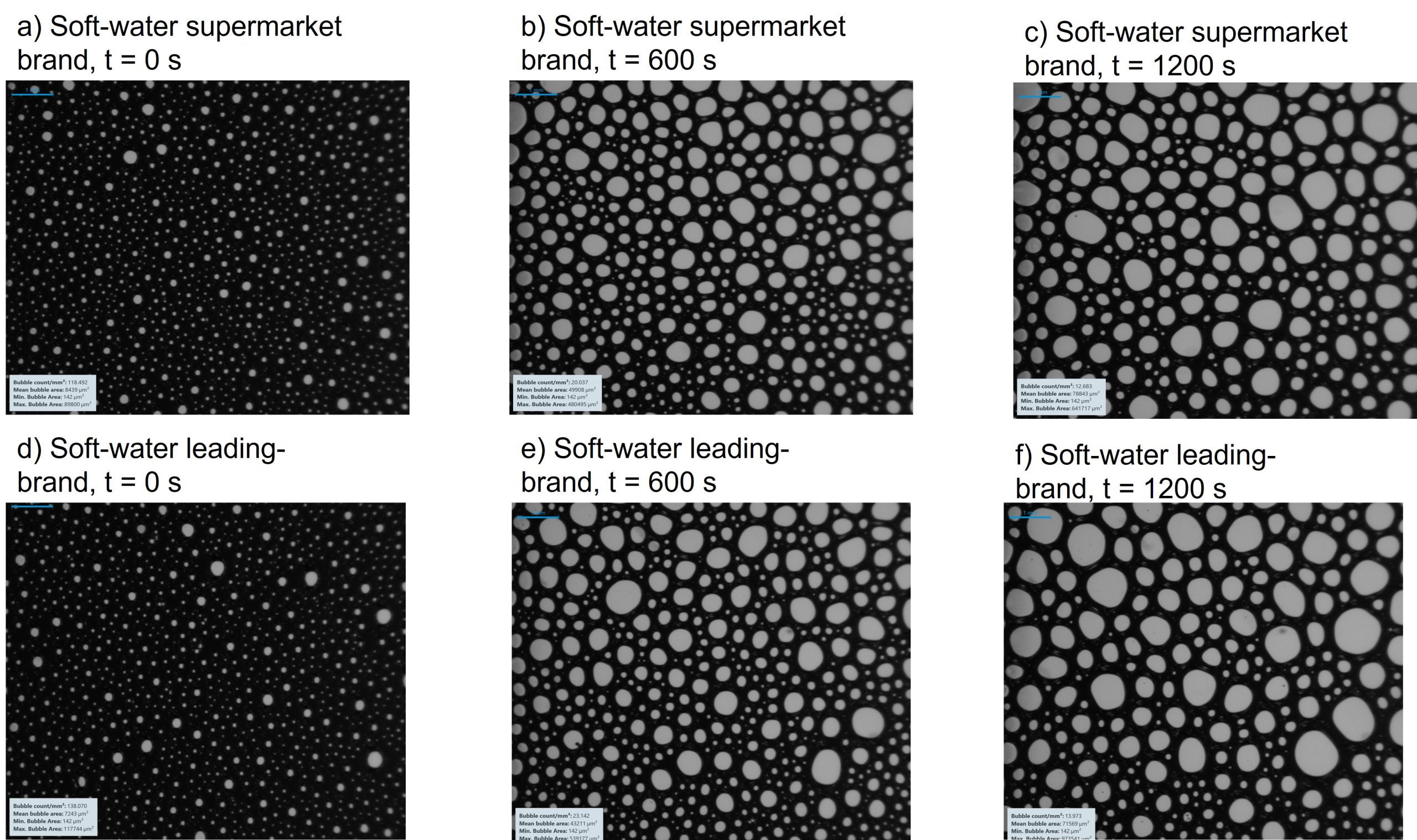
Putting the bubble count and mean bubble area data together, it can be surmised that a foam formed in soft water has smaller bubbles, with more bubbles per unit area compared with the foam formed in hard water. In addition, the soft water bubbles break down more slowly than the bubbles formed in hard water. It could therefore be concluded that hard water does have an impact upon the quality and stability of a foam, and that differences between brands are more apparent when hard water is used.
Conclusion on detergent foamability
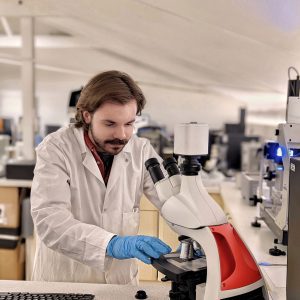
Dynamic foam analysis has been successfully used to compare and contrast the foamability of a supermarket-own and a market-leading laundry detergent brand. It has also been shown that hard and soft water have a significant impact upon the foaming ability of the laundry detergents and the overall stability of the foam formed. This work is likely to be of interest to those working with foams, either developing stable foams or with anti-foaming agents.
For further information about this testing, and other testing regimes that we offer, please get in touch!