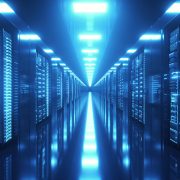
As processors are continually developed, their thermal design power is increasing exponentially, posing significant challenges in managing heat dissipation. Combined with the growing demand for AI-driven data centres, efficient cooling has become more critical than ever. Liquid cooling is emerging as a solution for high-performance processor cooling; however, its effectiveness can largely depend on the physical properties of the fluids used.
At the Centre for Industrial Rheology, we analysed commonly used direct-to-chip liquid cooling fluids, going beyond standard viscosity and thermal conductivity tests by looking at foam analysis. This case study highlights the importance of looking at foaming, as it leads to reduced heat transfer and potential problems with pumping.
Heat Transfer Fluids for Liquid Cooling
Heat transfer fluids for liquid cooling applications are generally based on deionised water, with specific additives used to prevent corrosion and provide freeze protection. While these additives provide essential performance attributes, they result in fluids with lower thermal conductivities and higher viscosities when compared to deionised water. As a result, formulators aim to use the minimum necessary concentration of additives to ensure optimal thermal conductivity and viscosity while ensuring adequate freeze and corrosion protection.
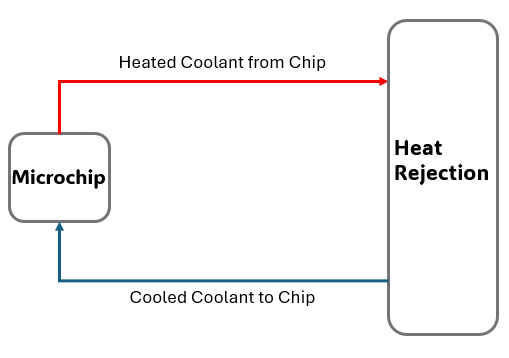
There are two main types of liquid cooling used in data centres: direct-to-chip and immersion cooling. Direct-to-chip works by circulating coolant through a cold-plate heat exchanger mounted directly onto heat-generating components. As the components generate heat, it is absorbed into the coolant which is then pumped through a closed-loop system to a heat rejection unit where heat is dissipated. Unlike traditional air-cooling methods that blow cooled air across entire server racks, often cooling areas that don’t generate significant heat, direct-to-chip focuses only on the components that generate the most heat. On the other hand, immersion cooling takes a different approach by submerging entire servers in a non-conductive liquid. This case study focuses on formulations utilised for direct-to-chip cooling.
Characterising Heat Transfer Fluids
To characterise the physical properties of heat transfer fluids used in direct-to-chip cooling, we selected three market-leading fluids used for PC liquid cooling. Their key claims and disclosed base ingredients are summarised in Table 1 below, with EK CryoFuel showcasing the boldest claims.
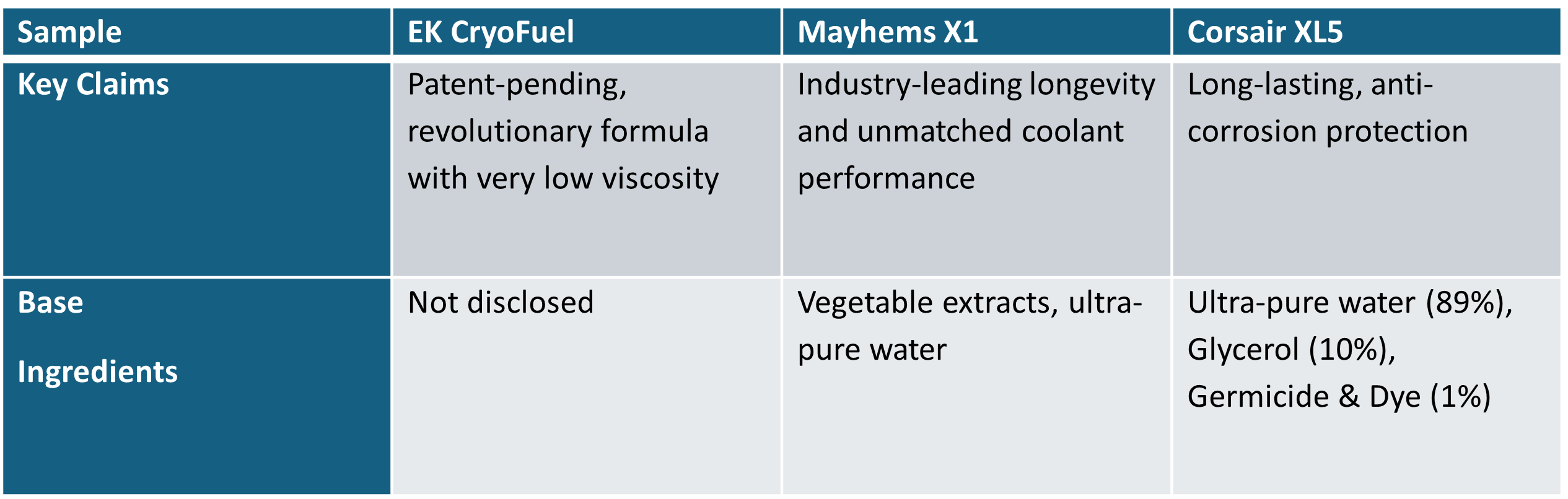
Viscosity of Heat Transfer Fluids
Measuring the viscosity of heat transfer fluids is crucial for the specification of pumps and assessing pumpability. A fluid with a lower viscosity can be pumped more easily, reducing the energy needed for pumping. This is particularly important in large-scale applications such as data centre cooling, where even small efficiency improvements can lead to significant cost savings. Viscosity measurements were conducted across a temperature range of 25°C to 60°C, representing typical operating conditions in liquid cooling systems.
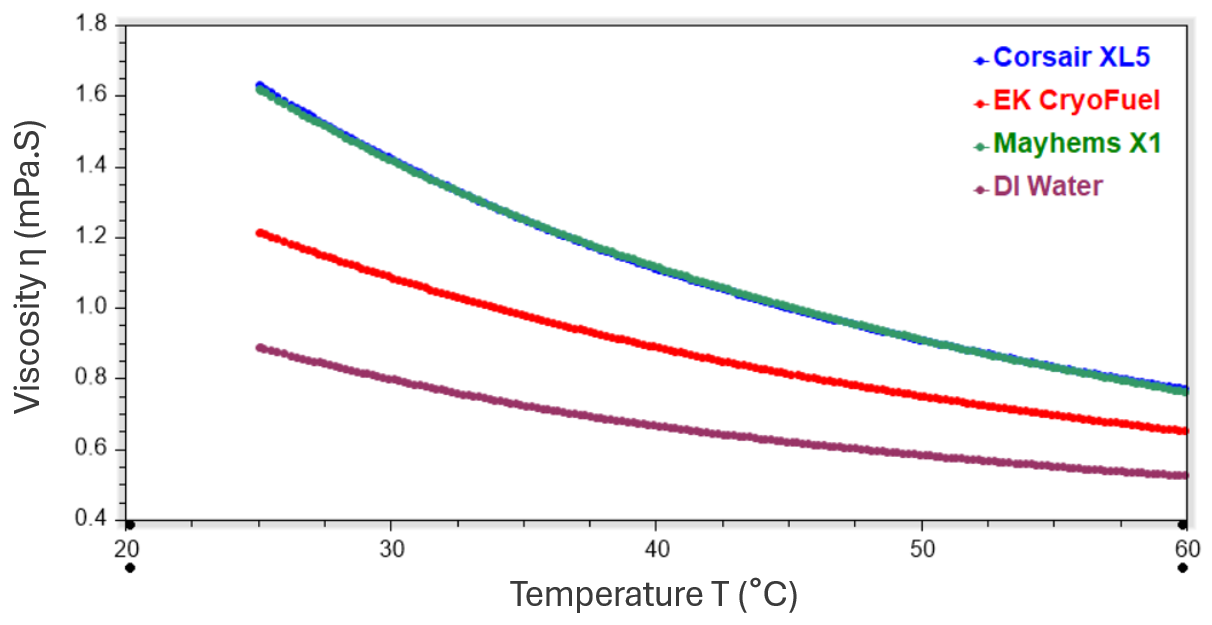
The results show that EK CryoFuel has the lowest viscosity among all samples, supporting its claim of being a “very low viscosity” formulation. Both Mayhems X1 and Corsair XL5 exhibited identical viscosity values across all measured temperatures. Further investigation revealed that Corsair XL5 is a rebranded version of Mayhems X1, rather than a unique formulation.
Thermal Conductivity of Heat Transfer Fluids
In addition to viscosity considerations, it is essential to maximise heat transfer efficiency. Fluids with higher thermal conductivities can more effectively transport heat away from heat-generating components. Thermal conductivity measurements were taken at 25°C to see if there were any differences between samples.
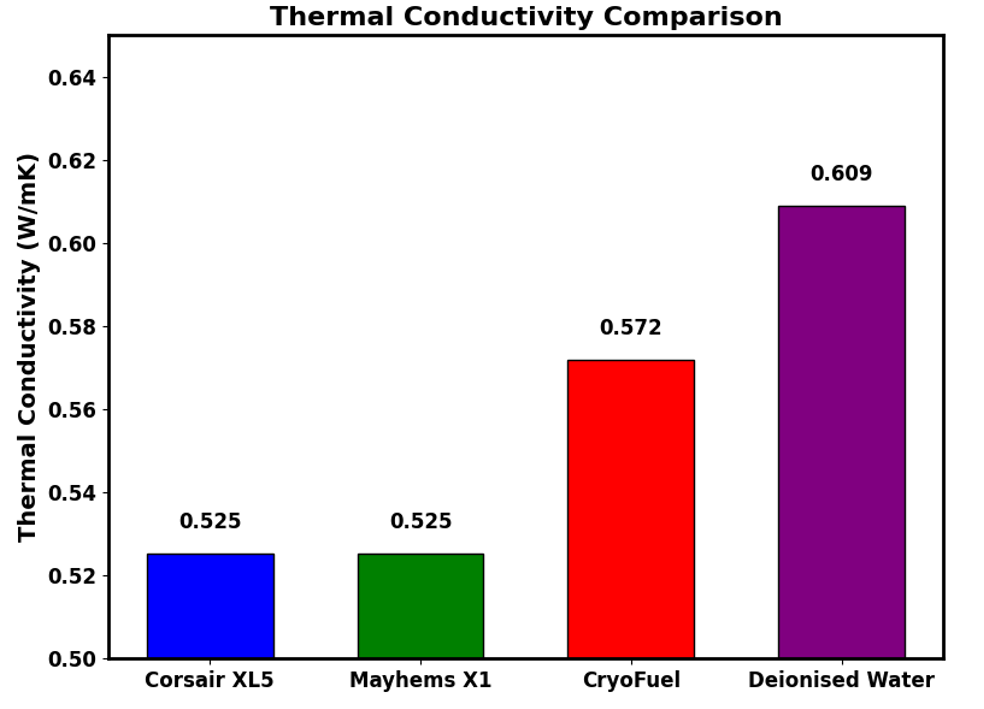
The results show that EK CryoFuel exhibited a significantly higher thermal conductivity compared to both Corsair XL5 and Mayhems X1, again supporting its claim of having the “best possible level of thermal efficiency”. As previously observed in the viscosity measurements, Corsair XL5 and Mayhems X1 displayed identical thermal conductivity values, further confirming they are the same formulation.
Foaming of Heat Transfer Fluids
Although EK CryoFuel has showcased its better thermal conductivity and viscosity, user reports of foaming issues with EK CryoFuel led us to investigate this issue with our foam analysis capabilities. The presence of dispersed air bubbles lowers the overall thermal conductivity of the fluid. As a result, even a fluid with superior thermal conductivity may perform worse if excess air entrainment occurs during operation.
Intending to benchmark how each sample reacts to air entrainment, we continuously sparged air into the samples at a rate of 0.3 L/min using our KRUSS Dynamic Foam Analyzer. The total liquid height was allowed to equilibrate and both bubble images and the total liquid height were captured at timepoints ranging from 100 to 275 seconds. By utilising image analysis software, we were able to quantify the voidage within each sample to determine which samples entrain the most air.
The sped-up video above shows how the samples are reacting to continuous sparging. Interestingly, we can see the adhesion of bubbles to the surface of the cylinder.
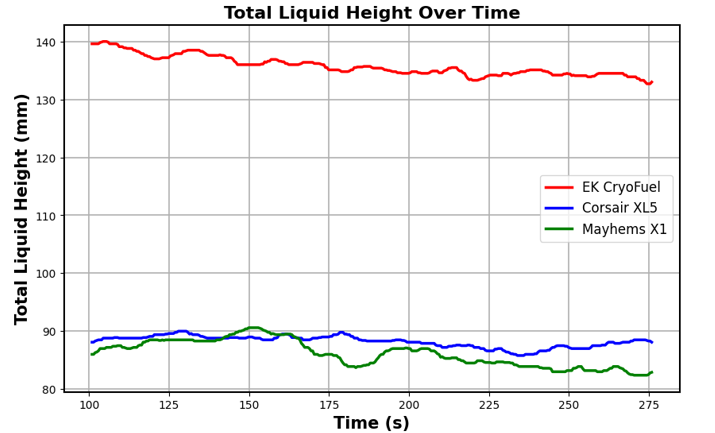
Figure 4 shows that EK CryoFuel resulted in a significantly higher total liquid height when compared to Mayhems X1 and Corsair XL5.
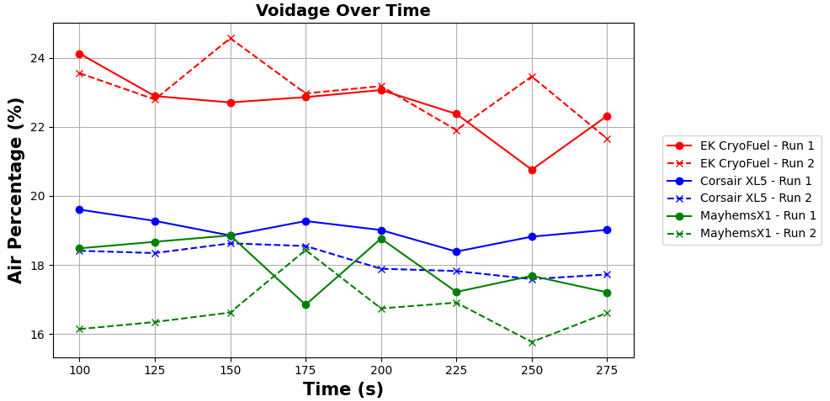
Figure 5 further illustrates that EK CryoFuel has a higher voidage than the other formulations, suggesting that it entrains more air.
To assess the significance of air entrainment and its impact on thermal conductivity, we applied the Maxwell-Eucken equation, which estimates the “effective” thermal conductivity of a liquid when gas bubbles are dispersed within it.
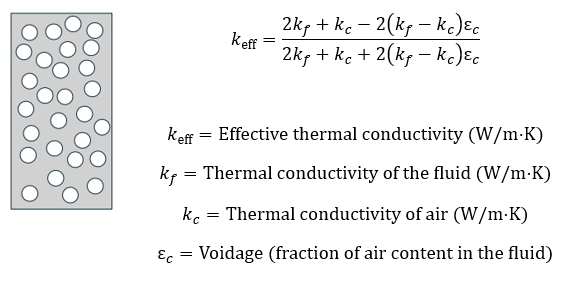
This equation accounts for voidage and the inherently lower thermal conductivity of air, providing a more realistic assessment of thermal performance where air entrainment is prevalent. It must be noted that we have only utilised this equation as a comparative tool.
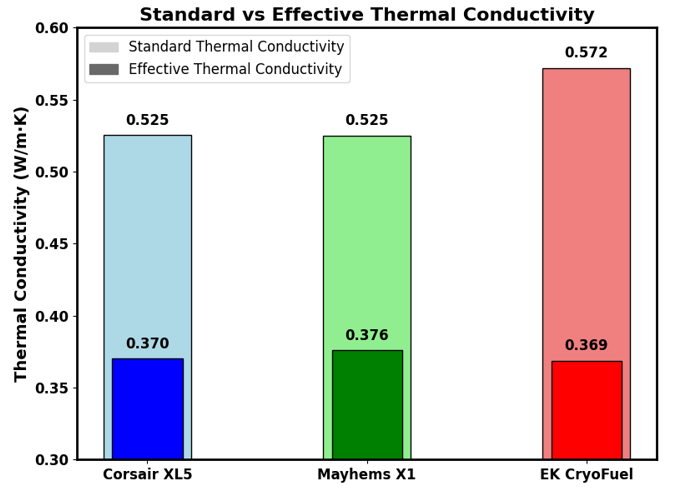
When voidage was factored into the calculations, the effective thermal conductivity of all samples was found to be nearly identical. This suggests that, despite EK CryoFuel’s superior standard thermal conductivity, its tendency to entrain more air compared to the other samples negates this advantage. This underscores the need to minimise foaming, particularly in demanding applications such as data centre cooling.
Summary
The market for liquid cooling is growing with increased thermal demand. This case study has highlighted the importance of physical characterisation to optimise formulations, ensuring the most efficient heat transfer. Particularly, we have showcased the importance of looking at air entrainment, as it can significantly hinder the effective thermal conductivity of heat transfer fluids. At the Centre for Industrial Rheology, our physical characterisation services provide rapid access to these insights.
We are keen to hear thoughts on our findings from those in the world of heat transfer fluids as we continue to research and develop our physical characterisation methods in this area.