The bulk rheology and interfacial behaviour of foams is extremely important to a number of industries, but their rheological behaviour is poorly understood. There are two aspects that can be subjected to the rheological investigation: the foams themselves, and the diluted liquid containing the foaming agents. Considering the rheological data generated may provide a way to predict foaming behaviour, for example the longevity.
Using bulk and interfacial rheological techniques, we have investigated the foaming behaviour of five baby bubble baths and outlined key differences in performance between them. This study will be of interest to process engineers, researchers and formulators in fields ranging from food and beverages to slurry processing to pharmaceuticals.
Foams and foaming behaviour
When using a bubble bath, one of the main sensory features is the look and feel of the foam bubbles generated. Poor foaming, or poor stability of the foam, can have a negative impact on the customer experience and can significantly affect a product’s market performance.
Contact us to arrange a lab tour and discuss rheological techniques with our experts
The foam is generated due to the dispersion of gas within the aqueous phase, but in order for the foam to be stable for an appreciable timescale a surfactant needs to be added. Surfactants are chemical compounds that have a hydrophilic head and a hydrophobic tail and lower the surface tension of a liquid at an interface, either liquid-liquid or gas-liquid. Lowering the surface tension is important as it allows the interface to resist external stresses and provides flexibility. The hydrophilic head group resides in the liquid phase and the hydrophobic tail group reaches into the air pocket, surrounding the air bubble and stabilising it within the coating liquid. The hydrophobic tails on the outside of the bubble prevent the air bubbles from agglomerating and rising to the surface to escape.
The stability of the foam depends upon two main factors:
- The tendency of the liquid films make the foam to drain and become thinner;
- The tendency of the foam to rupture as a result of random disturbances.
Evaporation and gas diffusion through the films may also affect the foam’s stability, therefore the surfactant(s) used can have a significant impact on the final foam.
Probing foam structure and stability
Bulk rheology is a useful tool for probing the stability and structure of the foam. Interfacial rheology, a useful partner to bulk rheology, can scrutinise an interface e.g. liquid–liquid or liquid–gas. Two useful parameters that can be determined at the interface are surface tension and viscoelasticity. Viscoelasticity can be sub-divided into two constituent parts:
- Elastic modulus (E’): The energy at the surface (or interface) that is recoverable
- Viscous modulus (E’’): The loss of energy at the surface (or interface) through spontaneous relaxation processes
The ratio of the viscous modulus to the elastic modulus, and the magnitude of the viscoelastic modulus (which takes into account the contribution of both viscous and elastic moduli), provide valuable insight into an interface’s rigidity.
Five bubble baths specifically marketed for babies were selected and a number of rheological tests were performed. In particular, we were interested in determining foam strength and stability using oscillatory techniques as well as surface tension and viscoelastic properties at the interface.
All samples were prepared at a ratio of 1:10 with de-ionised water and mixed using a magnetic stirrer. For foam preparation, the samples were placed in a foaming pot and pumped 100 times over a 30-second period immediately prior to loading onto the rheometer.
Foam stability
The stability of the foams created through a defined sparging process was assessed by measuring the height change of the foam in a cylinder over a period of 30 minutes. During the study there were visual changes in the foams, suggesting a structural alteration. For example, when the foams were first prepared the bubbles were small and the foams had a similar consistency to shaving foam. However, upon ageing, the bubbles clearly coalesced and the foam structure became more open Figure 1. Unfortunately, however, the difference in foam height between samples over 30 minutes was negligible, and no useful data could be gathered. We, therefore, turned to rheology to probe these structural changes in more detail.
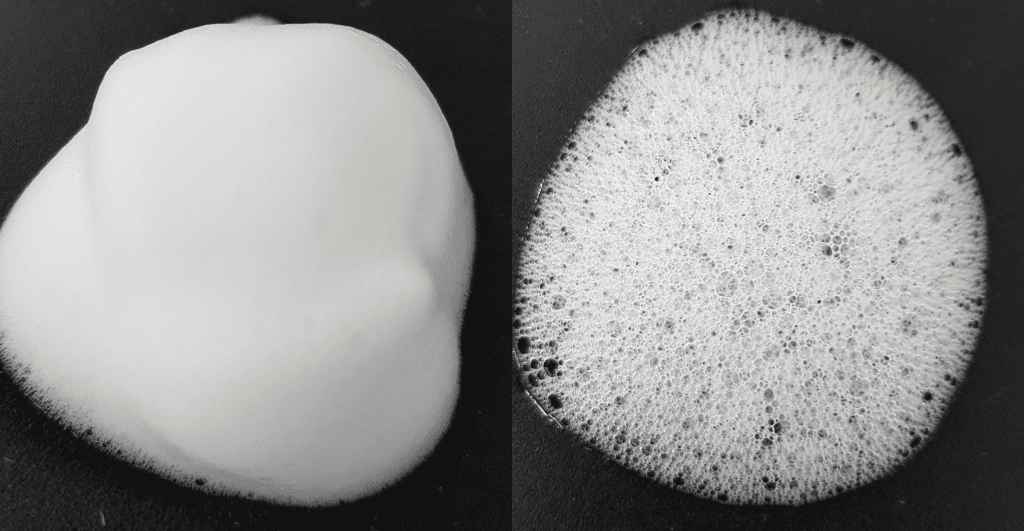
Foam strength and rigidity: Rheology measurements
An oscillatory stress sweep showed how the strength of the foams differed between brands. Collecting oscillatory data allowed for the identification of the linear viscoelastic (LVE) region where the stresses applied did not cause the breakdown of the microstructure. The end of the LVE is where the sample stops displaying Hookean solid (where the stress is proportional to the strain) and Newtonian liquid (where the stress is proportional to shear rate) behaviour. At this point, any stress applied cannot be easily correlated with any micro-structural properties.
Comparing the complex moduli of samples when the foams were initially prepared it was noted that most of the foams had a similar rigidity, Figure 2. However, there was one clear outlier: bubble bath D, where the complex modulus was noticeably lower than for the other samples and the end of the LVE was at a lower applied stress compared to the other samples. The smaller complex modulus indicated that bubble bath D had a less rigid structure compared to the other samples and required less stress to induce the breakdown of the microstructure. Bubble bath E had similar rigidity to the other samples, but the end of the LVE region was at slightly lower stresses than for samples A, B and C.
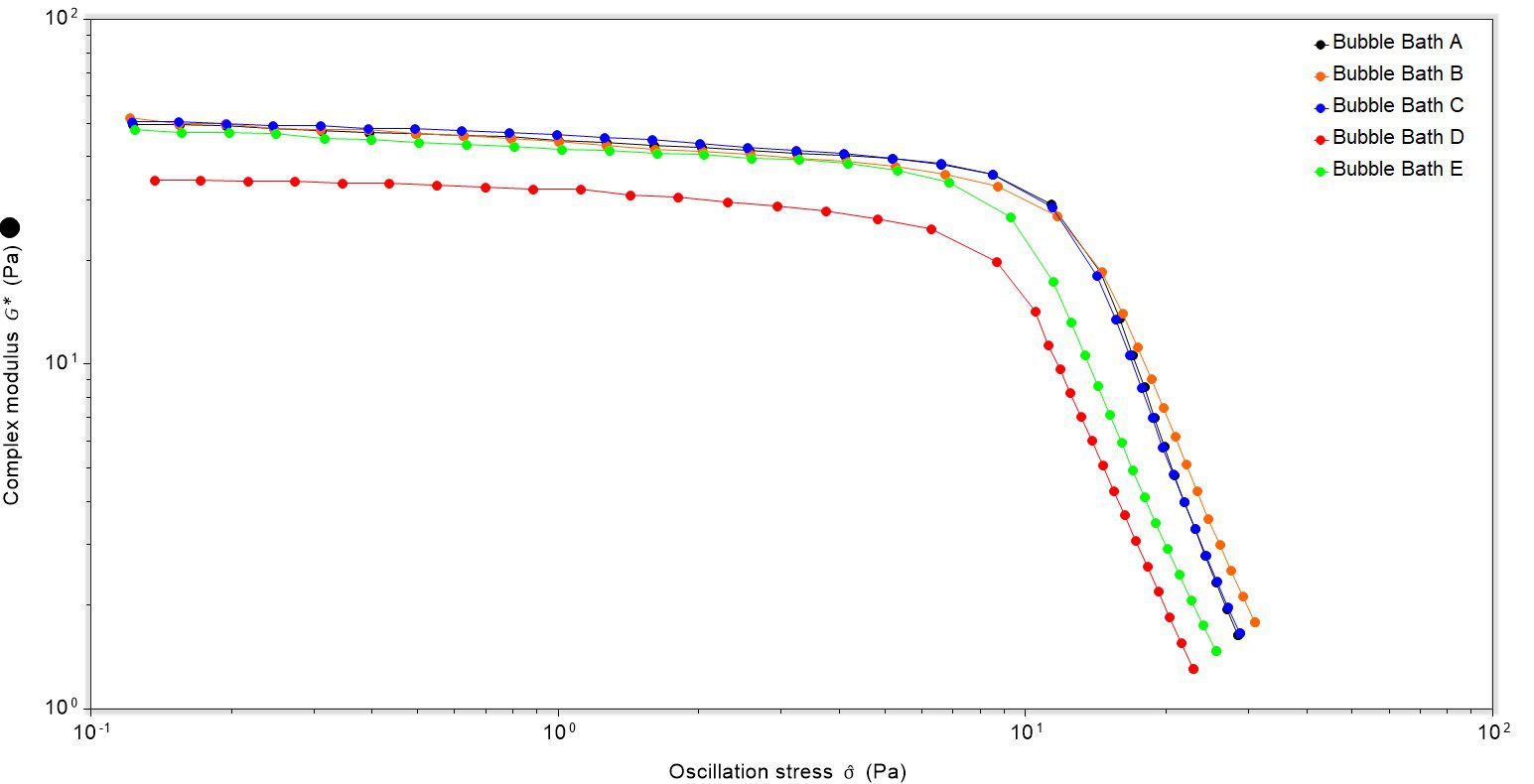
Quantifying foam structure change over time
Looking more closely at the change in storage and loss moduli over time also revealed some interesting behaviour. Foams were prepared as before and an oscillatory stress sweep was undertaken on samples at t = 0, 5, 10, 15, 20 and 30 minutes. It was noted that all the foams decreased in rigidity over time, usually at a constant rate. Representative data of samples A to E at t = 0 and t = 30 minutes are presented in Figure 3. At t = 0 and t = 30 minutes, the complex moduli are all broadly similar with one exception; bubble bath C maintains a much more rigid structure upon ageing. Comparatively, the rigidity of bubble bath C after 30 minutes is similar to the other samples after 10 minutes suggesting that the longevity of bubble bath C is better than for the other samples.
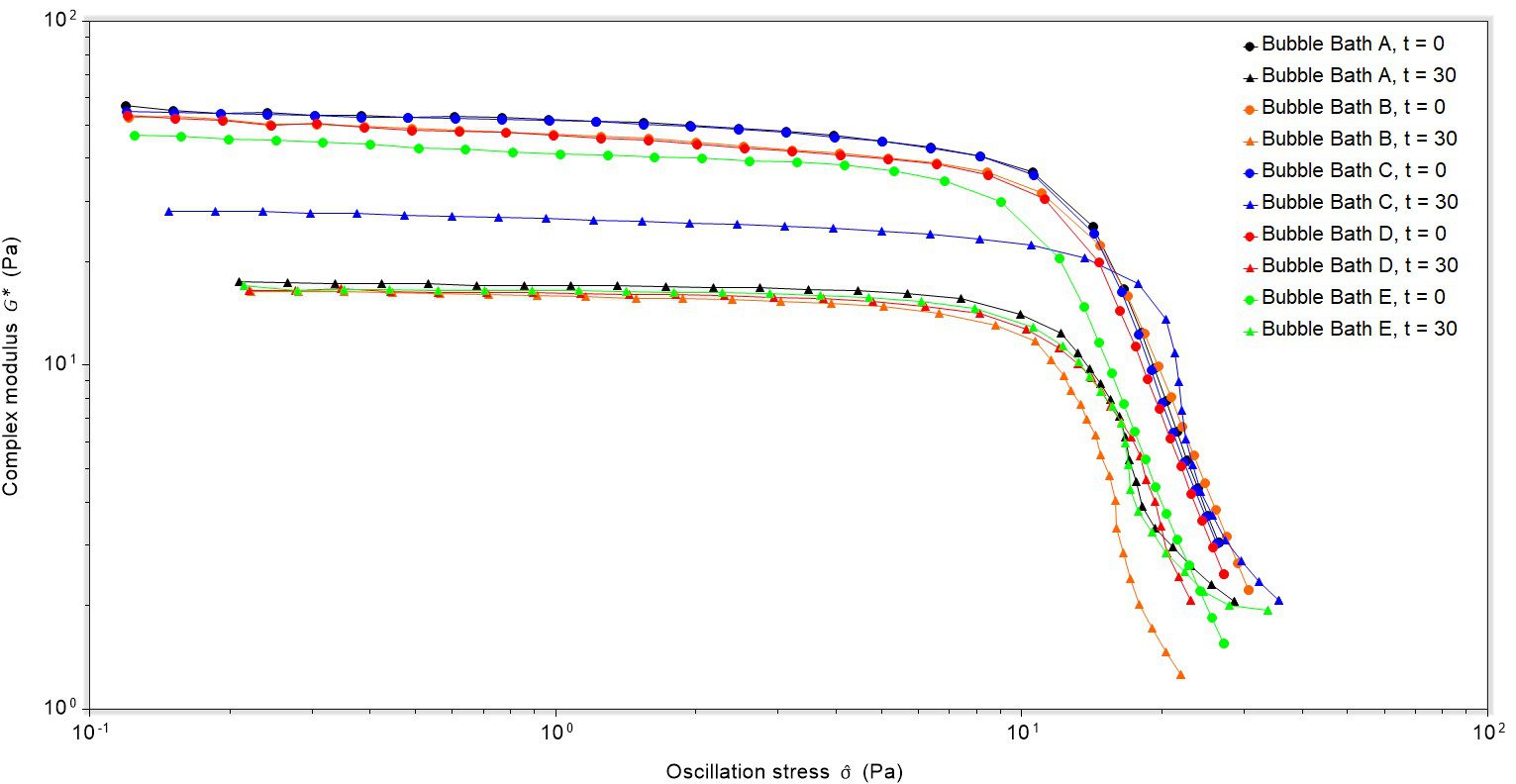
During the study, storage and loss moduli were also collected. Interestingly, the loss moduli all showed a significant uptick, or overshoot, prior to yielding. This uptick was noted as the same time as a significant decrease in the storage modulus. A representative example is shown in Figure 4. This is known as the Payne effect and was first observed in filled rubbers by Payne in the 1960s. The Payne effect has been observed in several plastic soft materials including glasses, gels, emulsions, suspensions, microgels and foams but there is no single rheological explanation for this phenomenon.
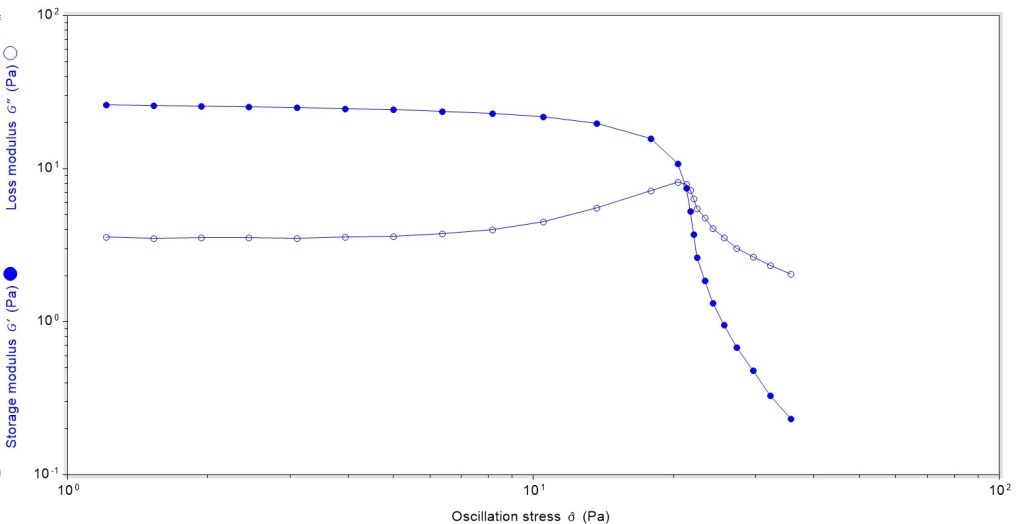
Investigating the interfacial viscoelastic properties of the mother liquids
Although looking at the structure of the foams provides valuable information relating to the rigidity and yield point, consideration of the interface surface tension and viscoelastic properties is also important. Both these measurements were collected using drop-shape analysis methods.
Completing a dynamic interfacial rheology measurement, namely an oscillating pendant drop, allows us to derive the elastic (the energy at the surface (or interface) that is recoverable, E’) and viscous (the loss of energy through spontaneous relaxation processes, E’’) moduli for each sample. These can be combined to give an overall viscoelastic modulus. Unsurprisingly, all samples had a lower surface tension than water (~72 mN/m at 25 °C). These data show that sample A has the lowest surface tension, and sample D the highest. However, the difference between each sample is fairly small.
Comparing the data, in most cases the viscous modulus was larger than the elastic modulus, suggesting liquid-dominant behaviour, Figure 5. The exception was bubble bath B where the elastic modulus was larger. Bubble bath C was an outlier, for a number of reasons. Bubble bath C had:
- The largest overall viscoelastic modulus, whereas the other bubble baths tested were very similar;
- The largest viscous modulus;
- The second smallest elastic modulus in comparison to the other bubble baths tested;
- The largest overall difference between the viscous and elastic moduli out of the samples tested.
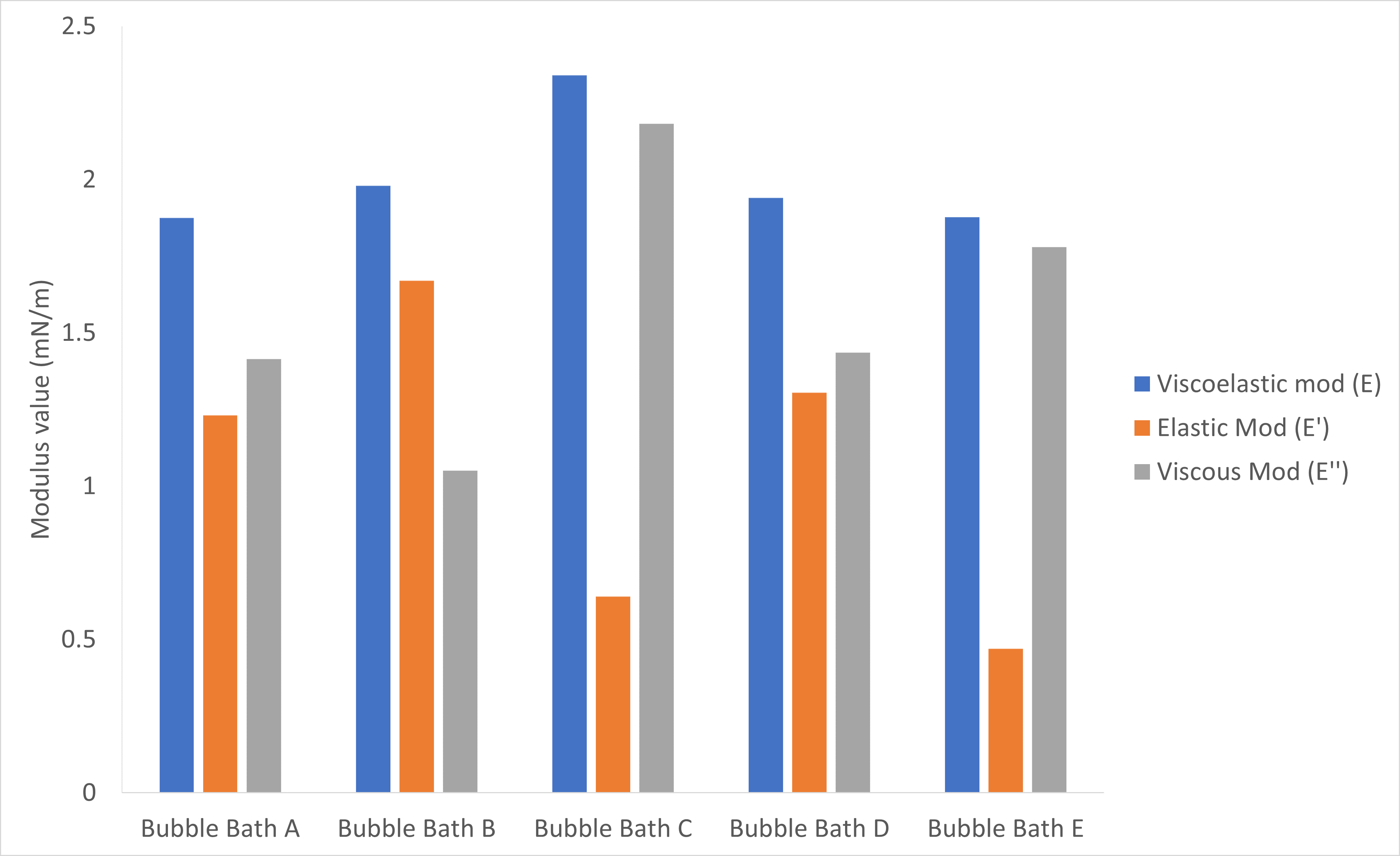
In summary, we have investigated the foam strength and interfacial characteristics of five baby bubble baths. Bubble bath C had bubbles that maintained this highest rigidity over the time period of testing, and when viscoelastic data were collected bubble bath C had the largest overall viscoelastic modulus, the largest viscous modulus, and the largest difference between the viscous and elastic moduli. Although these results may be coincidental, they may provide a starting point for the prediction of foam longevity and allow for rapid screening of solutions to streamline R+D processes.
For further information about these tests, or the range of tests that we offer, please contact us.