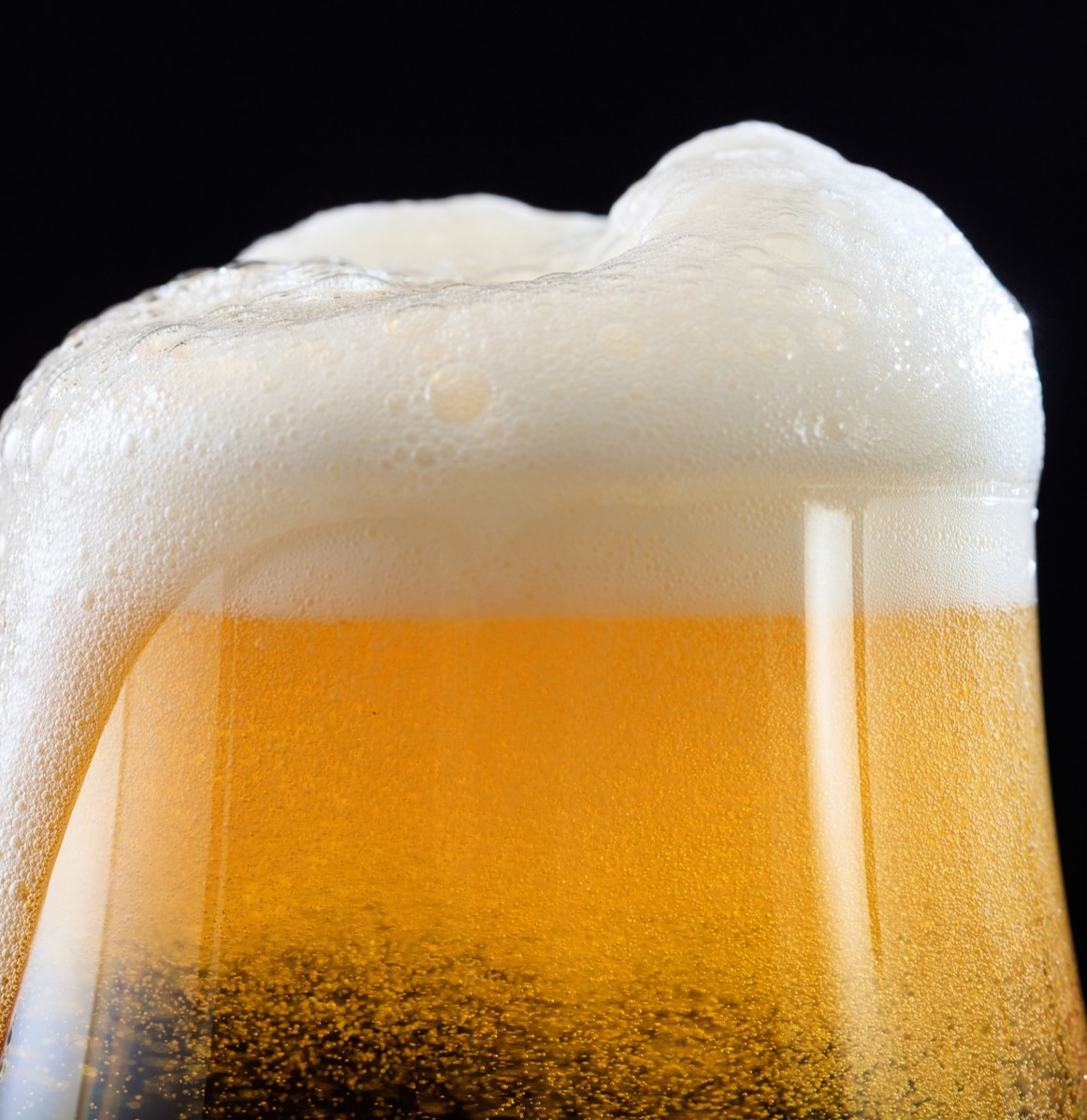
Optimum interfacial rheology properties can impart stability in foams. In simple terms, robust, elastic films surrounding bubbles tend to reduce liquid drainage, rupture and coalescence. Our laboratory provides expert interfacial rheology measurements to capture and quantify these properties for researchers aiming to accurately predict and optimise foam stability.
Foams play a critical role across industries—from food processing and cosmetics to enhanced oil recovery and advanced materials. Techniques such as Dynamic Foam Analysis offer powerful direct measurements of foaming, bubble size distribution, and foam stability. Interfacial Rheology measurements enhance these analyses by allowing detailed interrogation, comparison, and benchmarking of foam films’ physical properties, enabling formulators to rapidly test the impact of formulation and ingredient choices for optimum stability.
What is Interfacial Rheology?
When we think of rheological properties, we are usually considering bulk rheology, the elasticity and viscosity of the three-dimensional mass of material. However, elasticity and viscosity also act at interfaces, gas/liquid ones, in the case of foams, or liquid/liquid interfaces in the case of emulsions. These characteristics directly influence foam stability by governing drainage rates, coarsening behaviour, coalescence, and ultimately, the longevity and collapse of foams. Interfacial rheology measurements focus on understanding how these films respond to deformation.
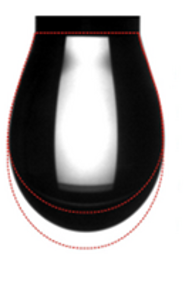
Interfacial Rheology Testing
Pendant drop shape analysis – also known as optical tensiometry – is commonly used to measure surface and interfacial tension. By fitting a mathematical model to the silhouette of a pendant drop, we determine the tension at the interface. The oscillating pendant drop method – the technique behind dilatational interfacial rheology measurements – extends this approach by expanding and contracting the droplet size to cyclically stretch and compress the interface. From the change in surface tension as a function of the change in surface area, it is possible to extract a modulus (i.e. rigidity) of the interface. With a knowledge of the phase lag between the surface area and surface tension, we can easily resolve out the elastic and viscous contributions to the overall modulus.
Applications of Interfacial Rheology
Some of the materials we have analysed recently include:
- Toothpastes
- Plant-based vs. synthetic surfactants
- Beers
- Plant-based milks for barista applications
Many examples of the successful exploitation of interfacial rheology for foam stability prediction exist in academic research. For example:
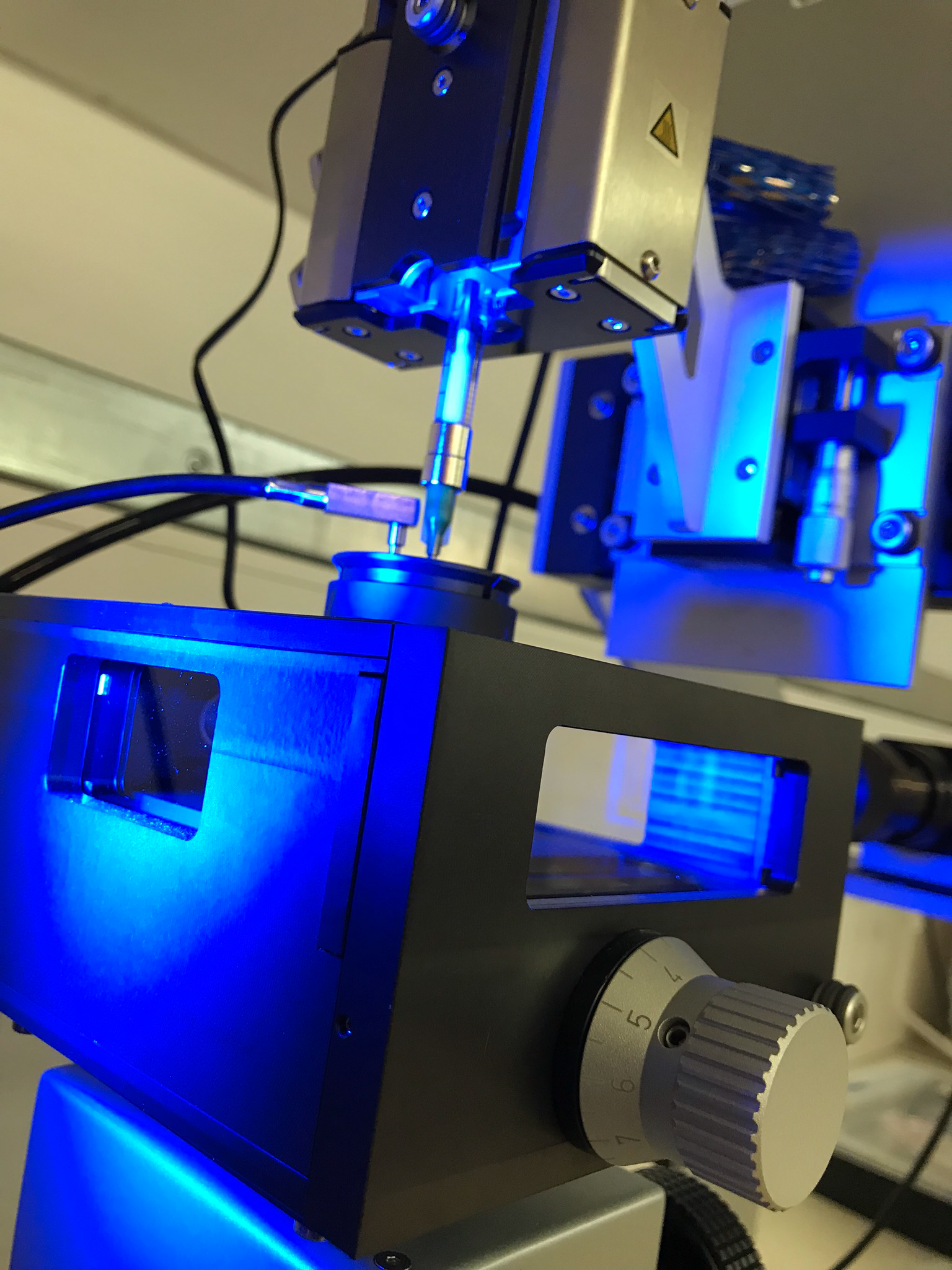
Yao et al. found that dispersed particle gel (DPG) particles at interfaces formed extremely elastic interfacial films, significantly improving foam stability by resisting drainage and coalescence. Their study highlighted that the presence of these DPG particles provided robust mechanical barriers at bubble interfaces, reducing bubble merging and liquid drainage, thereby extending the foam’s lifetime considerably compared to conventional surfactants [1].
Li et al. revealed that sulfobetaine surfactants create highly elastic films that enhance foam stability, particularly when combined with polymers, thus optimising formulations for enhanced oil recovery. They showed that the synergistic interaction between sulfobetaine and polymers significantly strengthened the foam films, resulting in improved resistance to environmental stresses like temperature and salinity, critical for effective performance in oil recovery operations [2].
Brown et al. demonstrated that foams stabilised by chain-like silica particles exhibited remarkably slow drainage, attributed directly to the stronger, more elastic interfacial network compared to spherical silica particles. Their findings indicated that particle shape plays a crucial role in foam stability, as the chain-like particles formed interconnected, rigid structures at the interface, effectively delaying drainage and bubble coarsening processes [3].
In summary, by utilising interfacial rheology measurements to characterise the rigidity and elasticity of air/liquid interfaces, researchers and product developers across multiple industries can accurately predict and optimise their formulations for foam stability.
References
[1] – Yao X, Zhao G, Dai C, Wu Y, Lyu Y. Interfacial characteristics and the stability mechanism of a dispersed particle gel (DPG) three-phase foam. Journal of Molecular Liquids. 2020 Mar 1;301:112425. Available from: Interfacial characteristics and the stability mechanism of a dispersed particle gel (DPG) three-phase foam – ScienceDirect
[2] – Li Y, Sheng Y, Peng Y, Ma L, Gao W, Yan C, Liu X. Effect of hydrophilic silica nanoparticles on foam properties of mixtures of silicone and hydrocarbon surfactants. Chemical Engineering Science. 2023 Jul 15;276:118769. Available from: Effect of hydrophilic silica nanoparticles on foam properties of mixtures of silicone and hydrocarbon surfactants – ScienceDirect
[3] – Brown N, de la Pena A, Razavi S. Interfacial rheology insights: particle texture and Pickering foam stability. Journal of Physics: Condensed Matter. 2023 Jun 23;35(38):384002. Available from: Interfacial rheology insights: particle texture and Pickering foam stability – IOPscience