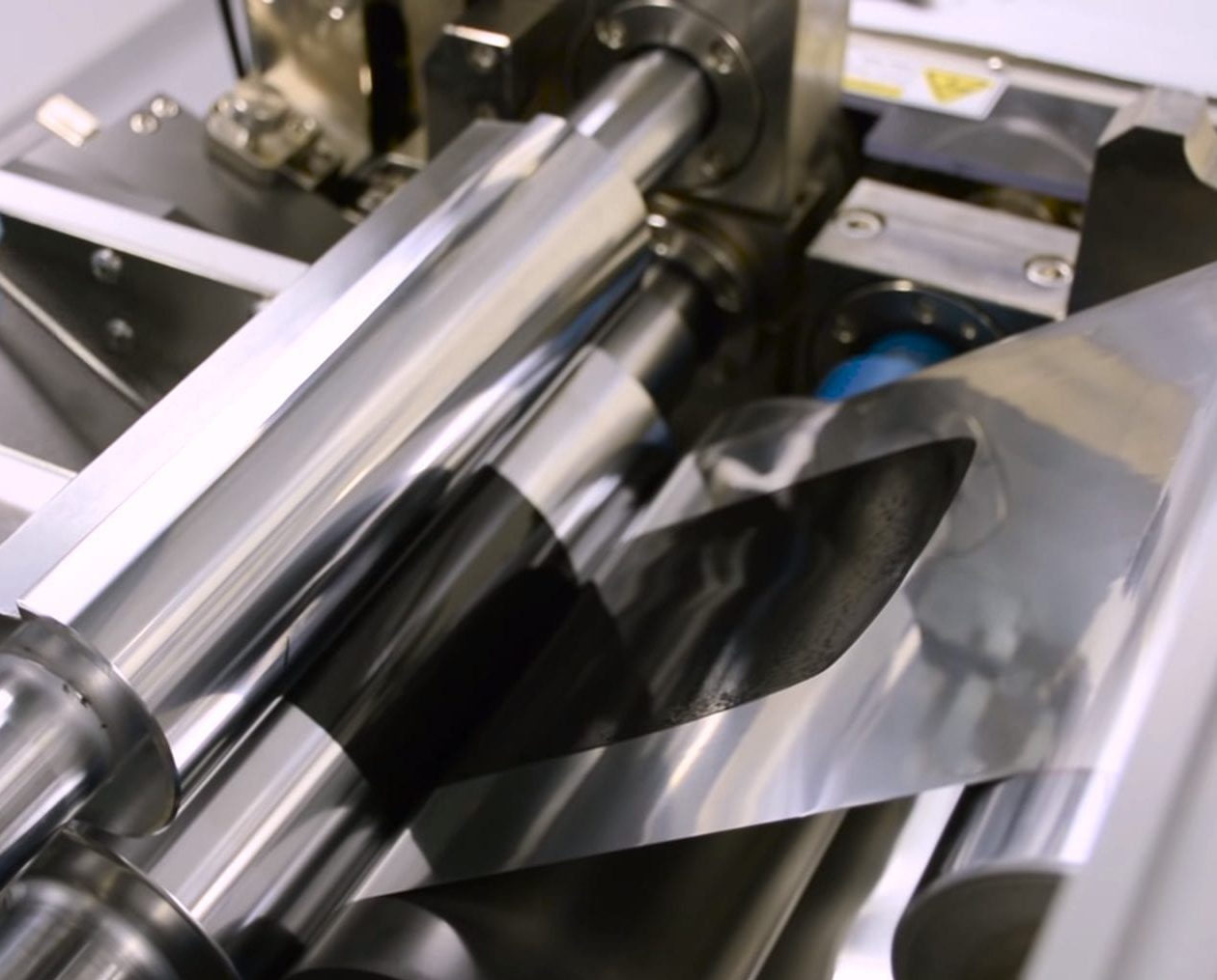
Formulating and printing electrode inks without knowledge of their rheology is like driving in the dark without headlights – you might reach your goal but it’s risky and uncertain. No researcher or process developer should be relying on a simple viscometer to tune their ingredient selection or process parameters.
We offer a powerful toolkit of test methods for comprehensively characterising the flow properties of printed electrode materials. These materials include anode and cathode slurries and inks along with a range of conductive and resistive thick and thin-film pastes.
Printed electrode manufacturing is a dynamic field that drives innovation in batteries, fuel cells, and hydrogen electrolysers. With ever-increasing demands for efficiency, durability, and performance, understanding and optimising the materials involved is more crucial than ever. In this article, we delve into three advanced characterisation techniques—Rheology, Rheo-Impedance Spectroscopy, and Rheo-Microscopy—that are revolutionising how we approach printed electrode manufacturing.
The Importance of Electrode Ink Rheology
Electrode inks and slurries are complex formulations whose performance during storage, handling, and coating relies heavily on their rheological properties.
Storage behaviours: On storage it is essential that the ink maintains a stable structure to avoid phase separation or sedimentation. Elevated viscosity and the presence of stabilising interparticle or polymer structures help deliver suspension stability.
In process behaviours: When it comes to handling and the coating process, the dynamic behaviour of the slurry becomes even more critical. Under shear during pumping or application, shear thinning behaviour is highly beneficial as it allows the slurry to flow easily through equipment. Following coating, the ink must rapidly recover its original structure after the shear force is removed, ensuring that the coating remains uniform and maintains a desirable distribution of solids throughout.
Together, these rheological properties ensure that the electrode ink not only performs well during production but also contributes to the overall quality and performance of the final electrode.
Rheology of Electrode Inks
Inks and slurries for printed electronics can be described as complex fluids that exhibit a range of process-relevant behaviours, including:
The test method protocols we perform to comprehensively characterise electrode inks includes:
Controlled shear viscosity profiles
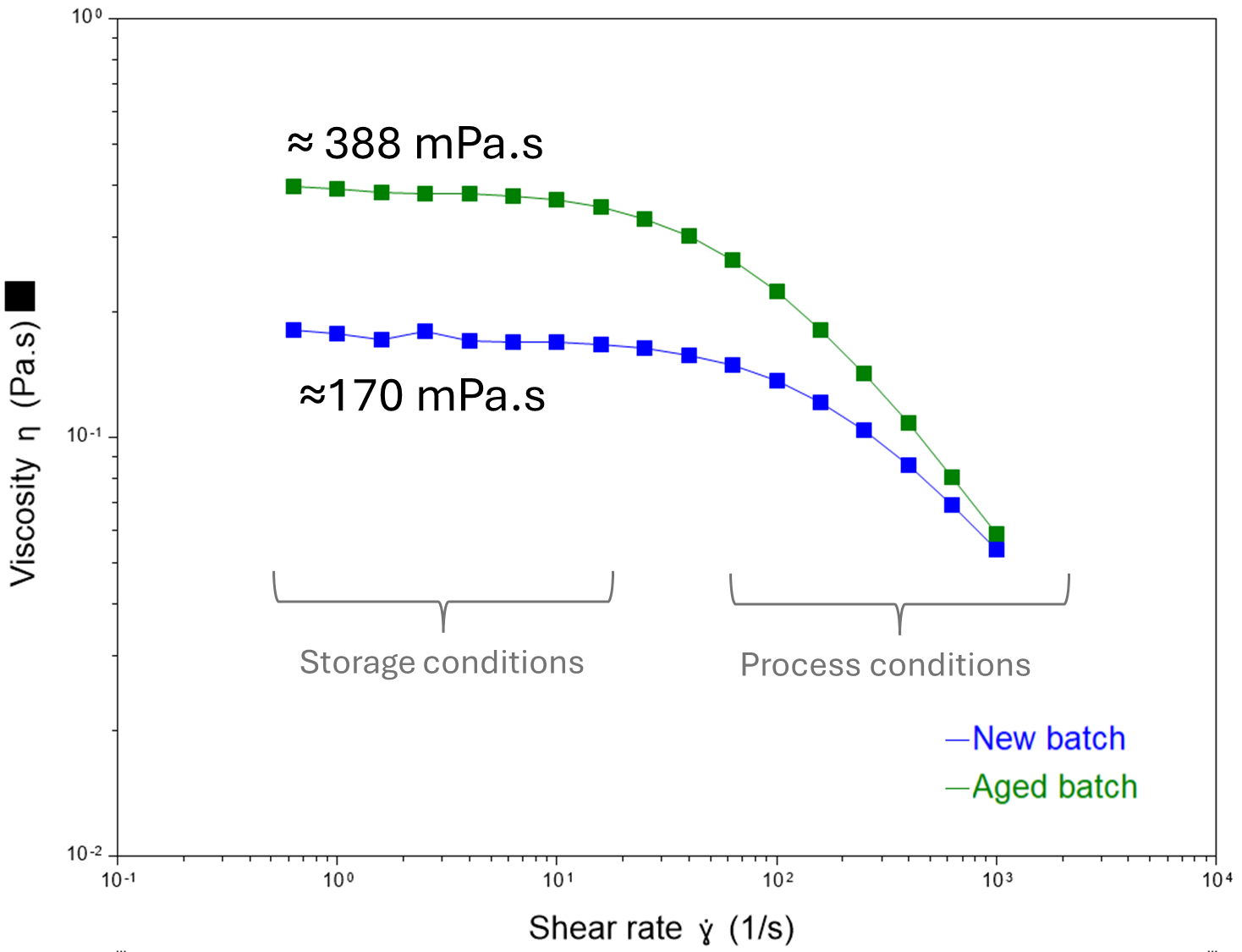
Viscosity measurements across a range of shear stresses and shear rates enable the characterisation of flowability across both process-relevant conditions, where non-Newtonian, shear thinning will be significant, but also the gathering of extremely low-stress “zero-shear viscosity measurements. Zero-shear viscosity can be thought of effectively as the “at-rest”, shelf or storage viscosity condition.
Oscillatory stress or strain amplitude sweeps
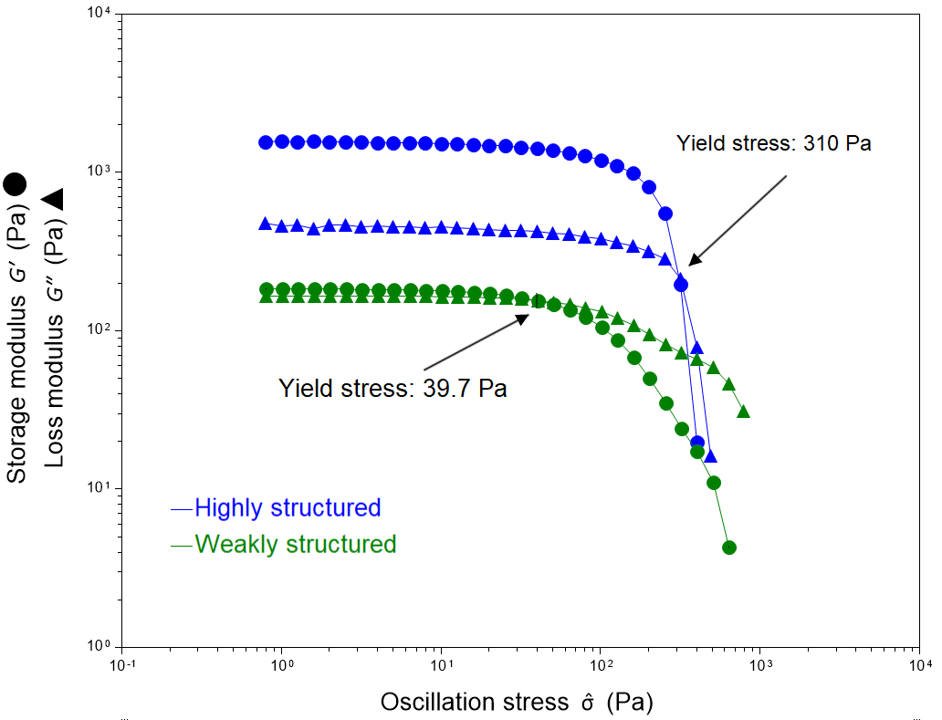
These measurements entail the application of small amplitude deformations or stresses to a sample to probe the elastic structures created through interparticle interactions. From this, the viscoelastic properties of storage and loss modulus are obtained. By incrementing the applied stresses or strains, the strength of structures can be elucidated in the form of the linear viscoelastic limit (the first sign of structural disruption) and yield stress or flow point, the stress required to initiate significant flow.
Oscillatory frequency sweeps
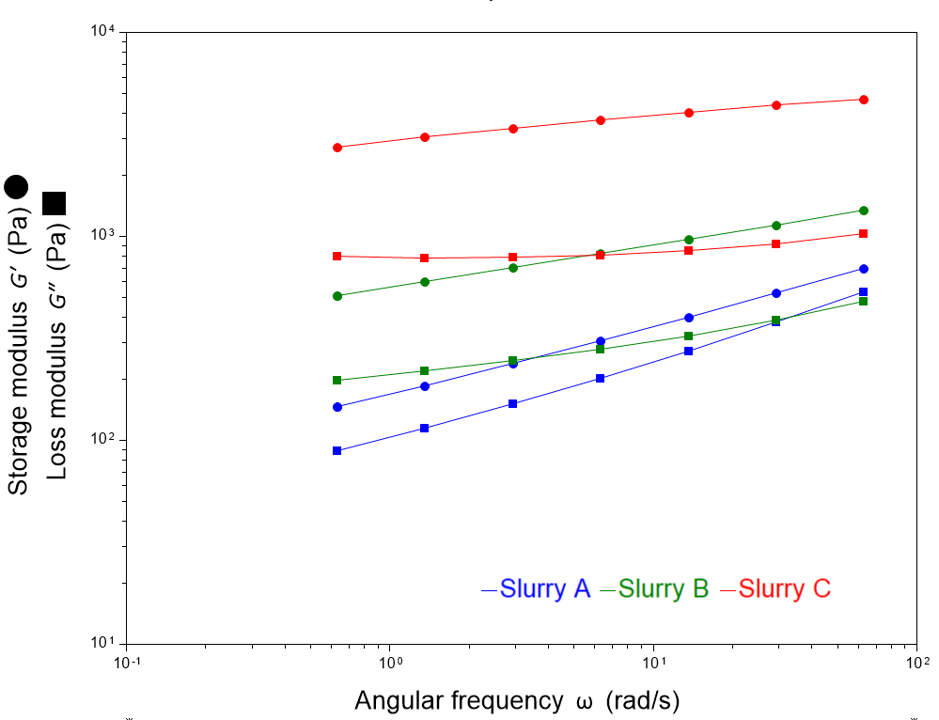
Frequency sweeps impose small amplitude oscillations across a range of frequencies to assess the integrity of ink structures and identify any “relax-ability” in that structure that may lead to creeping flow.
Three-step thixotropy profiles
Three-step thixotropy measurements observe the breakdown and subsequent recovery of viscosity or structure, following the application and subsequent removal of shear. The three steps comprise an initial conditioning step at low shear, followed by a high-shear disruption step then finishing with a return to low shear as the recovery is followed.
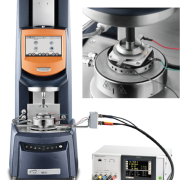
Combinatorial Rheology: Simultaneous techniques bringing unique insights
Rheo-Impedance Spectroscopy
Rheo-IS is a novel technique for characterising electrode inks that combines impedance spectroscopy, a tool for interrogating microstructure by observing its response to applied electrical current, with the application of shearing and the gathering of rheology data throughout. Such scanning of a wet ink, rather than the dried, cured coating, brings the ability to identify how the shear of a coating process, and the subsequent structure re-assembly, manifests in terms of final particle dispersion and arrangement.
Rheo-Microscopy: Visualizing Microstructural Dynamics
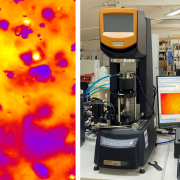
Rheo-Microscopy brings a visual dimension to the analysis of coating materials by capturing real-time microstructural changes under shear. This technique provides a window into how the material’s internal structure evolves during processing, bridging the gap between microscopic behaviour and macroscopic properties.
In summary, Rheology, Rheo-Impedance Spectroscopy and Rheo-Microscopy deliver a wealth of materials insights that the ink formulator or process developer can exploit to take their work to the next level.