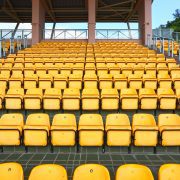
Thermoset polymers are vitally useful in the manufacture of both consumer products and in industry. Few materials meet the requirements of being able to change their phase state from an easy to handle fluid to an incredibly strong solid in an irreversible manner.
The ever-increasing demand for thermosets in a greater variety of applications necessitates sensitive and accurate measurement and profiling methods to capture thermoset performance and processing characteristics. Our lab specialises in performing rheological, dynamic mechanical and thermal analyses on soft materials including thermoset polymers.
If you would like to discuss rheological characterisation of your thermoset, please feel welcome to contact us.
Introducing Thermosets and Thermoset Rheology
Thermosets undergo a non-reversible cure, making practical trials highly time sensitive, difficult, and wasteful. High temperature, high sensitivity rheological profiling allows for precise, accurate and fast measurements of thermosets across their operating temperature range using only millilitres of material. Thermosets come in many forms, but generally share similar behaviour – starting with drop in viscosity up to a gel point, then rapidly hardening into a stiff solid.
A good thermoset transitions through each of these stages seamlessly and predictably and needs to meet the following requirements specific to its intended application:
- Easy to handle: either as a free flowing powder, or relatively low viscosity fluid
- Transitions at a reasonable temperature: This could be a temeprature range just beyond what is expected for the object to experience environmentally, or be designed to set due to environmental influence.
- Transition within a reasonable timeframe.
- Set to a required strength and hardness.
- Keep form once set.
Rheology can be used to help understand and predict the final product thickness, uniformity, adhesion, porosity, cure profile, temperature sensitivity, and many other key quality attributes. Helping to build a picture of the processing performance of your thermoset across a range of operating temperatures, timescales and mechanical situations.
Viscosity – An Unignorable Factor for Thermosets
A low viscosity can be useful in permitting easy handling, however it is a commonly known and somewhat intuitive fact, that as a material’s temperature increases its viscosity decreases which can be a difficult balancing act to negotiate when formulating a thermoset. Heating is a necessary step to induce curing, yet the inherent reduction in viscosity has the potential to cause drainage from a mould or pre-preg and can lead to a variety of other of production defects. Understanding the temperature-dependent viscosity of your thermoset is vital to ensure that the product handles as a customer would assume, or if specific material handling behaviours are required for unique applications.
Producing viscosity measurements for thermosets can be challenging, however. Many measurement systems are unable to achieve and maintain the required temperatures or measurement sensitivity. Traditional methods for measuring viscosity, such as rotational or capillary rheometers, can apply large destructive strains to the sample. These measurements are useful for the material in its liquid state but become less and less relevant as the material is heated and hardens. Ascertaining complex viscosity from non-destructive oscillatory measurements allows for the measurement to relate directly to a low stress situation, such as immediately post deposition.
Oscillation: Profiling the Cure of Thermosets
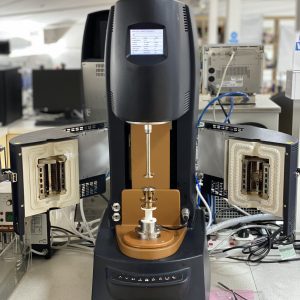
Oscillatory rheology applies small, non-destructive oscillations to a material and measures the mode of resistance to that applied force. Once the material is prodded, does it store the stress and bounce right back or is the deformation permanent? Generally, the answer is a combination of the two, with the ratio changing based on a whole host of factors such as temperature, time, stress and frequency. The ability to apply a non-destructive force to the sample is vital to ensure that your measurement doesn’t change your result; less delicate measurements might disrupt the sample, dramatically affecting the cure.
Oscillatory measurements are used to generate two primary measurements: G’, the storage or elastic modulus and G’’, the loss or viscous modulus. The two measurements in tandem explain a material’s resistance to deformation.
When we push the material, it resists being pushed. That resistance is made up of a reversible resistance, movement that is recovered once the stress is removed and irreversible resistance, permanent deformation unrecovered once the stress is removed.
By applying small oscillatory stresses to a sample, while ramping temperature, we are able to track the modulus values and examine whether a sample is displaying liquid or solid like properties. The value at which these two values crossovers is a crucial indicator of curing.
Quality Control of Thermosets
As well as being vital to developing good thermosets and enacting efficient processing parameters, rheological measurements can provide vital and rapid quality control measurements for raw materials, finished thermosets and in particular, prepregs. Heat, moisture and time can all dramatically affect the performance of these materials.
Ideally, a prepreg should be stored only for a short amount of time and in a cold, dry environment. Any deviation from that can allow chemical reactions within the prepreg to begin prematurely during the curing stage. Rheological analysis of prepregs can help to identify bad or poorly stored batches and avoid large amounts of wasted product. Rheological analysis of raw materials can help prevent bad batches and ensure repeatable end products. Understanding a supplier’s thermoset properties can help to make process design decisions, and ensure the product is right for the process.
Analytical Services for Thermoset Polymers
Few materials present such a wide range of rheological behaviours and properties as thermosets. The transition from thermoplastic solid, to molten liquid, through a gel-phase and into a stiff solid are highly characteristic of thermosets. Rheological analysis of thermosets can provide key insights into processing, production and performance of the product. Combining results from rheological methods helps better describe the variety of observed physical behaviours as the thermoset proceeds through its chemical transitions. Rheological methods can also provide a route to rapid and accurate quality control metrics for raw materials, prepregs and thermosets.