Powders experience a multitude of challenges during transport, namely vibrations and bulk compression, but also temperature and humidity changes. Dynamic Powder Flow Analysis (DPFA) provides a direct measurement of the propensity for the vibration induced immobilisation of powders and bulk solids during transportation, be it air, rail, or road.
This study focuses on the vibrations powders experience in transport, explore our previous study looking at the effect of temperature and humidity.
Powder Samples & Method:
The Centre for Industrial Rheology procured three powders used across multiple industries that are regularly transported and are subjected to transport induced immobilisation: graphite, titanium dioxide, and cement.
Each powder underwent a powder flowability test both before and after consolidation through vibration. A dynamic powder flowability test involves a blade geometry descending and rotating within a vessel containing the powder. The measurement generated corresponds to the energy needed for the blade to rotate through the powder.
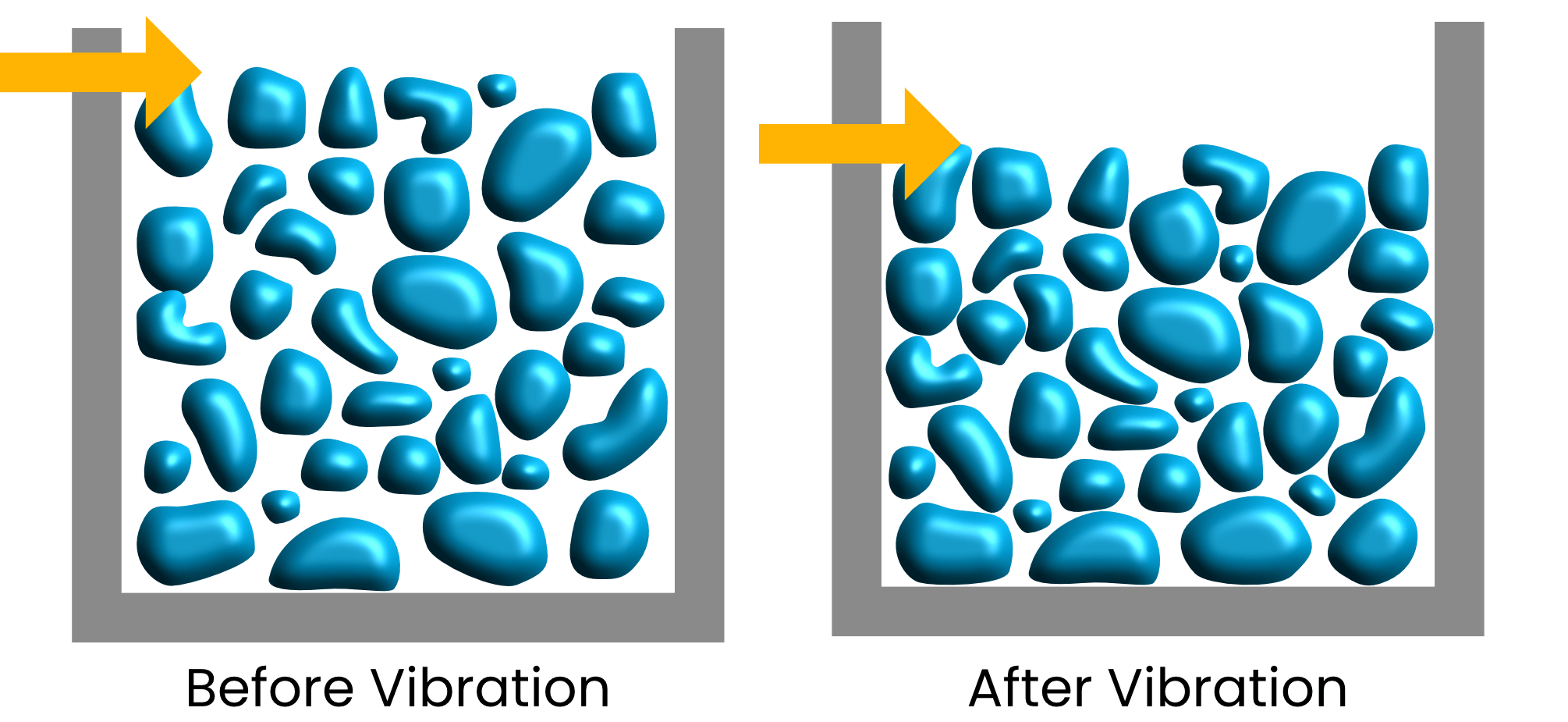
Powder Mobility Before & After Transport Induced Vibration
Relative to its initial value, graphite experiences the largest reduction in mobility whilst titanium dioxide demonstrates the lowest relative change. Before vibration, graphite had a mobility of 16.5. This decreased to 3.6 after vibration. titanium dioxide showed an initial mobility of 1.8, which dropped to 0.8 after vibration. Figure 1 illustrates the substantial impact of transportation on powder, highlighting that the powder received by customers differs from the powder that originally left the manufacturer’s factory.
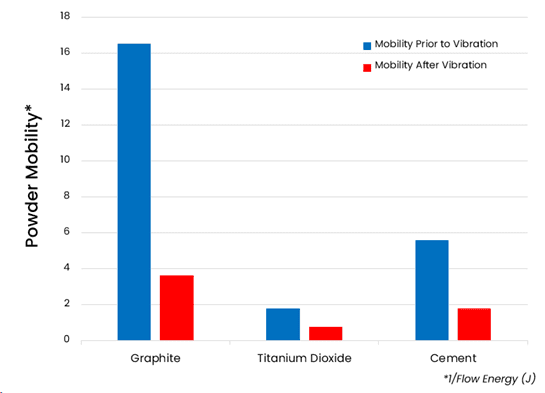
Post-transport Vibration Remobilisation
Transport alters the mobility of a powder, but for some samples these changes can be reverted.
We measured the mobility of each powder after 6 traversals to establish its remobilisation. All samples exhibit a degree of recovery, but titanium dioxide is the only sample to show total remobilisation.
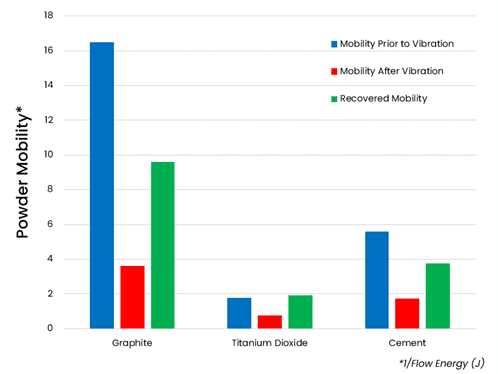
Relative to its initial value, cement has a higher level of remobilisation than graphite. The mobility value of cement prior to vibration is 5.6 and sees a decrease to 1.7 after vibration. The remobilisation value is 3.7. Graphite exhibits a remobilisation value of just 9.6 compared to its initial 16.5 before vibration.
With powders experiencing significant immobilisation during transport, it’s important for both powder manufacturers and those using powders to understand the degree to which a powder can be remobilised post-transport.
Conclusion:
In summary, DPFA proves effective in assessing the impact of transport on powder flowability. The examination of graphite, titanium dioxide, and cement reveals varying degrees of immobilisation during transportation.
These findings stress the importance of understanding how powder behaviour changes during transport for both manufacturers and end-users. DPFA offers direct measurement for predicting and addressing mobility changes, providing crucial insights for optimising powders to survive transport, and ensuring the quality of powders received by customers aligns with the intended product.