Physical powder characterisation can be a vital part of oral solid dose design. From advanced screening of end-product properties such as capsule fill or tablet hardness to processing problems like hopper dispensability, API/excipient segregation or dusting. Physical characterisation of an oral dose blend can be a key step to producing reliable, fast, and cost-effective processing conditions and creating high-quality, repeatable end-products.
Understanding the wide range of physical characterisation methods available enables formulators, process designers and contract manufacturers to select scale-up candidates, produce fail-proof processes and predict end-product performance for tablets or capsules.
Our lab provides a variety of physical characterisations for investigating the handling behaviour of powders and provides ongoing technical support to ensure you can make the most of the results we provide.

Flowability for Processing
Flowability is often at the forefront of the minds of anyone attempting to process a powder blend. While the core concept of getting a powder from point A to point B can seem simple, it can often leave people utilising a single characterisation method confused.
The most common method of powder flowability testing, shear cell measurements, help one to broadly understand how hard it is to get a powder moving by measuring the powders’ ability to slide – either against itself or against another material.
Dynamic powder flow measurements allow for the powder to be measured whilst it’s moving – if shear cell measurements provide an “activation energy” to get a powder moving, dynamic measurements tell us how hard it is to keep a powder moving.
Dynamic measurements also allow us to understand how the powder flows under a wide range of conditions, for example, while aerated, after being held at high humidity, or following a wet-granulation step.
Powder Stability
Powder stability can mean a lot of things – changes to particle size and shape as it is processes, aeration or deaeration, or segregation of smaller particles from the bulk are all common occurrences during processing, and all can be hard to predict in laboratory conditions prior to factory scale-up. Particularly for solid oral dose pharmaceuticals, where excipients tend to be fairly large and small API particles can act as flow-aids, segregation of the API from the bulk is dangerous and unacceptable.
This kind of testing can also be key to designing wet-granulation processes. By performing dynamic, constant measurements of the powder as it is forced to flow, we are able to identify changes in the physical properties of the powder as it is processed. This kind of testing allows for the identification of segregation, changes in flowability due to wet-granulation methods and help to identify wet-granulation endpoints.
Powder Characterisation for Prediction and Pre-Screening
Predicting how a powder will behave in end-use, after factory-speed processing or in an industrial scale hopper will always be a challenge. Especially so when API’s are expensive to produce, especially at a large scale. Repeatable and accurate measurements with small quantities of powder blends can help predict several factors.
Basic flowability energy can be an early predictor for tablet hardness, small scale dynamic measurements can be a useful tool for identifying endpoint granulation.
Powder properties can vary wildly based on often unpredictable factors, but by comparing an experimental batch with a known formulation, or raw excipient powder, it is possible to begin to predict how a powder will handle under more stressful conditions.
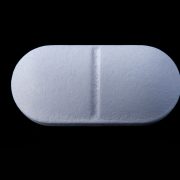
Tabletting and Capsule Filling
Flowability, both dynamic and static, are vital measurements for tabletting and capsule filling processes. Getting a powder into a capsule or tablet press and, keeping it there whilst a compressive force is applied, is often the make or break of an oral solid dose processing procedure, dictating the speed and efficiency with which the rest of the process can run.
Whilst flowability measurements are a vital characteristic to understand for this process, they are not the only factor to consider; powder permeability, the ease at which air is able to pass through a column of powder, can often be the limiting factor. Whether filling a tablet press or capsule, air must pass through the column of powder to allow space for the powder.
If a powder has poor permeability and the space is filled too quickly, a rush of air can push the powder out of the intended space. A high-permeability powder will allow the air to pass through without disturbing the powder, meaning processes can be run under higher pressures and at faster speeds. In some cases, a poorly permeable powder can lead to voids, ending in under-filled capsules or brittle tablets prone to snapping and capping.
Conclusion
Powder processing can be difficult and frustrating, with the added complexities inherent in oral-solid-dose powders only exacerbating these difficulties.
High potency, expensive API’s available in small quantities can often be prohibitive to factory-scale experiments, meaning pre-screening powder characterisation can be vital.
Understanding the characterisation methods available can allow for robust characterisation and in the end, allow formulators to produce and select powder blends that produce better end products and faster more efficient processing procedures.