Rheological profiling of potentially viscoelastic materials can provide a crucial early warning of troublesome high-shear onset elastic effects in manufacturing, providing the formulator or process developer with a valuable heads-up far in advance of expensive plant and resource selection decisions.
Feel welcome to arrange a chat to find out if your product has viscoelastic characteristics
If you’ve ever wondered why your lovingly-created formulation is proving such a challenge to pump or fill, despite the fact that its viscosity is just as low as all the other products in your range, then you may have succumbed to the insidious little nasty that is viscoelasticity, or, more specifically, timescale-dependent viscoelasticity and normal stress generation.
Many of today’s manufactured materials possess an elastic structure as a result of various mechanisms such as colloidal interactions of suspended particles or droplets. On the application of sufficient stress (the yield stress) this structure is disrupted and flow ensues. This is the typical “split personality” behaviour of a structured liquid; as long as sufficient stress is imparted these products present no particular problem for pumping or filling processes.
Viscoelasticity in surfactant and polymer solutions
However, another type of behaviour can arise in a slightly different class of materials that can pose quite a problem. Many liquid formulations are either thickened with high molecular weight linear polymers or formulated to generate certain surfactant structures in order to provide texture, lubrication or film-forming properties. An unwelcome accompaniment to these attributes is an onset of elasticity that only rears its head when we’re in a rush to move the stuff around, such as in the pumping and filling processes. A product can show all the signs of a well-crafted non-Newtonian liquid, with a generous dose of shear-thinning to impart the double-bonus of good stability and easy application and transportation – and yet it can display a number of unwanted behaviours during processing and filling.
Rod climbing can occur, where the material being mixed climbs up the stirrer or mixer shaft rather than forming a centrifugal vortex. On pumping from a tank into a small orifice such as pipework or a filling head unexpected back-pressures can lead to problems with pumps and seals. On filling, die swell effects lead to reduced clearances between the nozzle and container wall and stringing and poor cut-off can result in residual product coating both bottles and machinery.
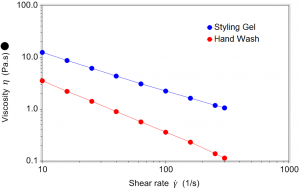
An understanding of the viscoelastic characteristics of a material can save time and money for formulators and process developers looking to ease and de-risk plant selection and commissioning. In concert with viscosity profiling, two very useful tests can identify the onset of elastic effects under high-shear conditions:
Normal stresses in viscoelastic liquids
Normal stresses are stresses that are generated perpendicular (i.e. normal) to the direction of shear that results from the reaction to the straightening of polymer chains under shearing.
It is the rapid relaxation of these chains on exiting a nozzle that leads to the die swell mentioned earlier. High normal stress growth under shear can flag up a potentially problematic onset of elastic behaviour under rapid deformation.
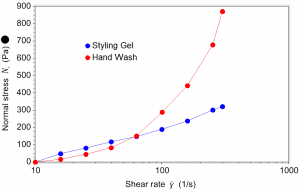
Oscillation Frequency Sweeps
In an oscillation frequency sweep a sample is exposed to small amplitude oscillatory (clockwise, then counter-clockwise) deformation across a range of timescales.
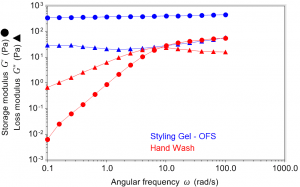
The relative proportions of elastic (solid-like) or viscous (liquid-like) response as the frequency of oscillation increases (i.e. timescale of deformation decreases) can highlight the onset of troublesome elasticity in a product.
The two methods described here can supplement the viscosity testing of gels, polymer solutions and surfactant systems to provide the product developer with tools to ease scale-up and process development for viscoelastic products.
Find out what other rheological methods can assist with your process optimisation, contact us now.