If you are looking at setting up a slot die system, or have a slot die system but are experiencing defects, understanding the rheology of your coating is key in preventing and minimising processing errors. Common errors such as bubbles, ribbing and wrinkles all have a foundation in the rheology, surface tension and dynamic wetting properties of the coating. Understanding those properties is key at all stages of your slot die process; whether you have a coating and are looking at slot die as an application process, or have a slot die set up and are checking to see if your coating formulation will work with your equipment.
Contact us to discuss our rheology and surface characterisations for slot die applications
Viscosity, Rheology and Surface Tension – Vital Information For Setting up Your Slot Die
The rheology of your coating is key when deciding the appropriate range of operating parameters including coating speed, flow rate, vacuum pressure, coating gap and liquid viscosity. Do you need an infinite cavity or coat hanger manifold? Will you be direct, tension web or curtain coating your substrate? Are you looking for a multi-layer process? Identifying the viscosity of your coating is a key first step to understanding your slot die requirements.
Manifold type will be determined depending on if your coating is Newtonian, with a constant viscosity, or Non-Newtonian where the viscosity of the coating changes depending on the shear forces being applied. If you are looking at tension web or curtain coating to achieve a particularly thin layer then shear thinning properties, where the coating’s viscosity lowers as stress is applied becomes important. Furthermore, thixotropic recovery, the time it takes for your coating to return to its resting viscosity after being sheared, will play an important role in the coating adhering to the substrate.
Surface Tension – Eliminating Edge Defects
As the pump switches from on to off for lane or intermittent coating, defects can appear as areas of thickness at the edges of the coated areas. These thick edges appear due to the surface tension, viscosity and viscoelastic properties of the coating.
At low viscosity surface tension largely dictates edge thickening. As the liquid constituent of the coating evaporates faster at the edges, more of the coating is drawn to these areas as an action of surface tension. This results in a thicker dry film at the edges of the coating. At higher viscosities, surface tensions role becomes less prevalent and shear thinning, thixotropic recovery and yield stress take over the process.
Viscoelasticity – Prediction of Die Swell
Viscoelastic coatings swell as they exit the slot die, potentially resulting in destabilisation of the menisci and introducing a range of defects. We can predict viscoelasticity by measuring normal stress generation during a shear rate sweep. A viscoelastic coating can store energy from the high stresses experienced during extrusion. After deposition, the energy from this stress in the coating dissipates over time, which can cause the coating to expand or contract. This movement after deposition can cause irregularities in film thickness.
Using Rheology to Minimise Chattering and Ribbing – Interfacial Analysis of a Coating to a Substrate
Chattering presents as long areas of increased thickness at regular intervals across the whole width of the deposited coating. This can be due to variations of pressure in the fluid delivery system or pulsed movements on the roller. Ribbing presents similarly to chatter, although it affects the length rather than the width of the coating. These defects can be minimised or eliminated simply with a coating that wets well and spreads once deposited.
Wetting and spreading is a complex process, and is a function of many properties such as surface tension, viscosity, viscoelasticity, yield stress and thixotropic recovery rate. A dynamic wetting analysis works in combination with rheological analysis looking at how the coating reacts to a “free flow” situation once the coating has been deposited onto the substrate. Using these methods it is possible to identify key characteristics that determine a “good” or “bad” coating in terms of wetting and spreading to minimise these defects.
Dynamic Contact Angle, Surface Tension and Viscosity – Minimising Air Bubbles
Bubbles can be a common defect in all types of coating processes, and slot dies are no exception. Small amounts of air can get between the leading and back-end menisci of the coating as it leaves the slot die. Once this bubble makes its way outside of the dynamic contact point it can present as areas where the coating is particularly thin or even missing from the substrate. Bubbles can be introduced as air is entrapped during destabilisation of either meniscus. You can eliminate these errors by maintaining a stable meniscus. Maintenance of a stable meniscus is the result of a combination of factors, including surface tension, dynamic contact angle and viscosity. By investigating the rheology of your coating you can begin to understand how the slot width, upstream/downstream coating gaps and attack angle of your slot die could be introducing defects into your process.
Rheology and Dynamic Wetting – Essential Information for Slot Die Design
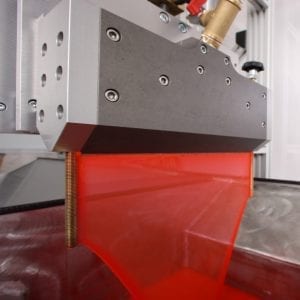
A firm knowledge of the rheology, surface tension and dynamic wetting properties of your coating can be of great benefit from conception and design of your slot die all the way through to defect identification and troubleshooting. A rheological profile can also be invaluable when determine the makeup of your entire slot die system, from the liquid pump to the die lip. Getting a coating with the correct rheological profile can help to simply minimise defects within your final product. Finally, knowledge of the rheological properties of your coating prior to a defect arising allows for quick diagnosis of defects allowing your process to continue with minimal disruption.
Let us know if you would like to discuss your requirements in more detail. Contact us now.