Rheology and surface tension: A toolkit of measurements for spray drying process development.
The rheological and interfacial properties of the feedstock liquid are critical physical properties that offer valuable insights for the spray drying process developer. The two key areas in which rheology and surface tension impact the spray drying process are in the droplet break-up phase and in the establishment of desired particle morphologies on drying.
Contact us to discuss how rheology and surface analyses can help optimise your spray drying process.
Influence of rheology and surface tension on droplet breakup
The viscosity of the feed solution has a significant influence on atomisation. A higher viscosity solution will require higher energy inputs to attain given volume flow rates from the atomizer and higher viscosities limit the turbulent flows available for breakup of the ejected stream into individual droplets.
It is often the case that the feed stock is not a simple liquid, but may exhibit one or more complex fluid properties. Non-Newtonian liquids, for example, such as suspensions, emulsions and polymer or protein solutions, often exhibit shear-thinning behaviour where viscosity is not a single value but rather it decreases with increasing shear rates.
Depending on factors such as the volume fraction of particles or droplets, or the concentration and molecular weight of any dissolved polymers, the viscosity dependence upon shear rate of non-Newtonian liquids can become significant. If measurements are to be performed to predict or model atomization processes or to screen batches of feedstock prior to spray drying it is critical that these are performed at elevated shear rates that are more relevant to the process, rather than under those shear conditions typically applied during simple spindle viscosity measurements.
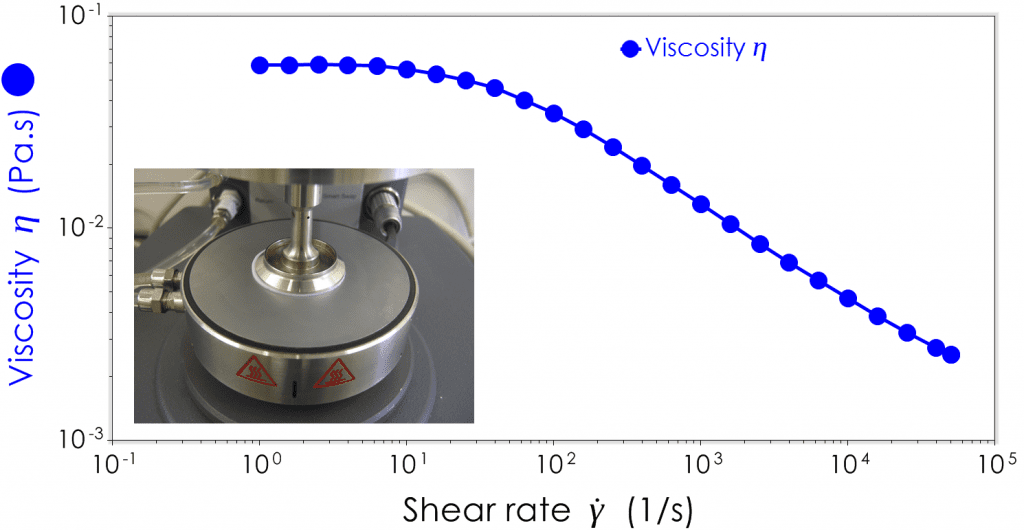
Viscoelasticity of spray dry liquids
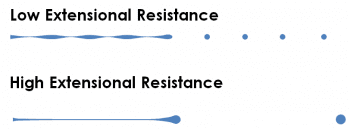
Elastic behaviours can also inhibit atomization and may therefore impact the spray drying process. A liquid containing a high-molecular weight linear polymer in solution can often display extensional elastic resistance that impedes the deformations necessary for “pinch-off” into smaller droplets to occur. Rheological profiling methods can deliver data that can predict such extensional properties.
Surface tension and droplet formation
During the atomization process an enormous amount of surface area is created. A 1 litre sphere of liquid, atomized to 20 micron droplets creates around 300m2 of surface area. A liquid with a high surface tension requires more energy to generate additional interface, and if the energy is not available due to viscous losses prior to stream ejection from the spray dryer nozzle larger drops result.
Viscosity and surface tension are both influenced by feedstock temperature so any measurement of feedstocks for comparative purposes should be performed under consistent and relevant conditions.
Doughnuts and Death Stars: Yield stress and spray dried granule morphology.
Slurries, suspensions and emulsions all display yield stresses; interactions between suspended particles or droplets generate a three-dimensional structure that impedes flow unless a stress that exceeds the yield stress is applied. The presence of a particle microstructure possessing such a yield stress has been seen to impact the drying droplet in two ways:
Firstly, significant structure may arrest surface tension-driven “spheronization”, resulting in irregularly-shaped dried granules.
Secondly, the presence of a permeable aggregated interparticle structure, and its accompanying yield stress, has been proposed to impede migration of those particles outwards from the centre of the droplet during drying.
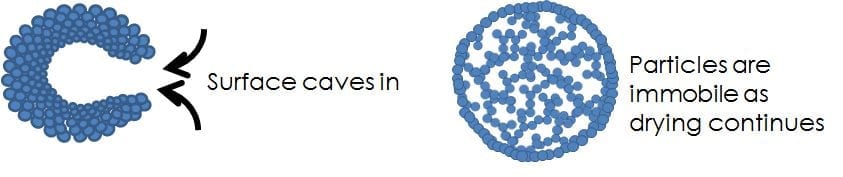
Migration from the centre and the subsequent formation of a rigid particulate shell around a droplet, has been seen to lead to collapses as the droplet shrinks, leading to doughnuts, “Death Stars” and other morphology irregularities. Suspensions of flocculated/aggregated interacting particles have been shown, therefore, to immobilise particles throughout the drop, resulting in a more spherical dried granule.
From Routine Spray Drying Analyses to Sophisticated Characterisation of Rheology and Surface Tension
The Centre for Industrial Rheology specialises in working with difficult materials, providing first class characterisation of physical properties, presented in a user-friendly format under short deadlines. We can provide routine characterisation to more powerful and sophisticated testing, and are well equipped to exploring novel approaches to physical characterisation. Whether you are interested in a fluctuating dynamic process, temperature dependency or an ageing related study, we have decades of expertise across a wide range of industries suited to solving technical challenges.
If you would like to discuss our full range of capabilities relevant to the spray drying process, please feel welcome to contact us.