Here are ten great ways savvy formulators, process designers and quality controllers are using our rheology results to gain an unfair advantage for their products:
1. Get a rheological analysis of your competitors’ products and compare them to yours
This is a great way to gain an advantage in a competitive market place. To formulate the best sensory and handling properties, application, coating or film-forming behaviour or storage stability you first must know, and quantify, where you are in relation to your competitors. Rheology profiling is a great way of doing this.
2. “Snapshot” the rheology of the perfect batch
If you’ve made the perfect batch, be it in the lab, pilot or production stage, rheology will enable you to capture those qualities and establish a benchmark, for the record, of the key qualities of your product. If you’re a formulator and you’re transferring to a contract manufacturer, or you are setting up a new factory to produce an established product, a rheology snapshot of how things should be can avoid all manner of difficulties and conflicts.
3. Screen cost-saving ingredients for their impact on an established formulation
Finding effective, low cost replacements for formulation ingredients can be an arduous task fraught with uncertainty. A profile of choice rheological metrics such as yield stress, zero shear and high shear viscosity and viscoelastic parameters such as storage and loss moduli are excellent tools for helping ensure the cheaper alternative you’d like to use will not adversely affect your product.
4. Establish viscosity build profiles for a heads-up on bulk storage and filling decisions
Viscosity build of emulsions, suspensions and gels following manufacture can lead to major processing, filling and quality control headaches. Establishing a rheology/viscosity build profile covering the hours and days following manufacture will help you make decisions on when to transfer to bulk storage and when to fill to final packaging.
5. Perform thermal and shear stress testing as an aid to stability studies
Performing rheological profiles before and after thermal and mechanical (i.e. shear) stress regimes is a great way to build confidence in a formulation in the early days of ageing studies. Furthermore, temperature cycling tests on the rheometer can identify reversible and accumulating irreversible changes in a product throughout multiple temperature swings.
6. Learn about the impact of cooling regimes on final product rheology
Crash cooling a small batch of emulsion can result in a very different final rheology compared to a slow cool of a full size production batch over several hours. Thermorheology investigations can help formulators and process developers predict, and deal with, susceptible formulations in the process design stage.
7. Avoid processing headaches with a heads-up on ‘difficult’ rheologies
High yield stresses, shear sensitivity, rapid viscosity build on standing or the onset of elastic effects with high shear can all present problems for the process engineer who needs to be able to mix, pump, store and fill the most challenging of materials.
8. Choose the right packaging and delivery method for your product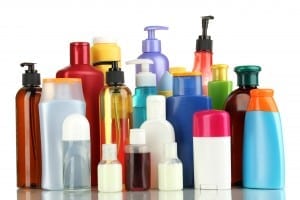
Container evacuation, pouring, spraying and squeezing are all influenced strongly by product rheology. Understanding the rheology profile of your product can enable you to make decisions to ensure a satisfactory product-packaging marriage long before costly commercial decisions are made.
9. Identify the equipment and accessories you need for in-house testing
Looking to set up a rheology testing function in-house but scared of wasting the huge outlay required for a typical research rheometer? A short program of outsourced testing will help establish a confident justification for investment, as well as ensure you identify the instruments and accessories you need without wasting a fortune on items that will sit in the cupboard unused for years.
10. Profile a coating or deposition process
The ability to deliver a coating material to a surface in an even manner, with a minimum of surface defects such as air entrainment, pinholes, brush marks or streaking, and then to have it remain in place without dripping, sagging or slumping, demands the correct rheology. An understanding of factors such as yield stress, thixotropic recovery rate, zero-shear and high shear viscosity can help the formulator here.